What is investment casting?
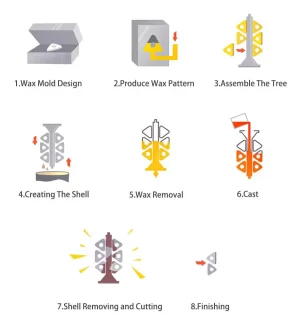
Investment Casting Processes
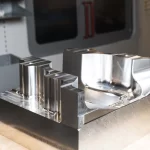
Mold design ⇒
Unless investment casting is being used to produce a very small volume (as is common for artistic work or original jewelry), a mold or die from which to manufacture the wax patterns is needed.
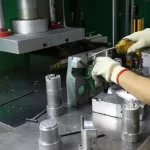
Wax pattern creation ⇒
For every individual casting produced through investment casting, a new wax pattern is required, making the number of wax patterns needed equal to the total number of castings. Wax injection machine will do the job.
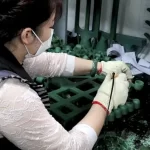
Assemble Wax Patterns Tree ⇒
Assemble the wax patterns to a gate or system. Multiple patterns are assembled to allow for large quantities to be produced at one time. This process will need workers do by hand and be very careful.
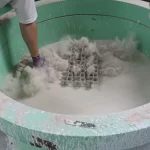
Shell building ⇓
creating a ceramic shell around the wax pattern to create a mold for the molten metal. The wax pattern is coated with a ceramic slurry, and repeated several times to create a thick, durable shell
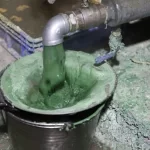
Wax Removal ⇒
Once the shell has hardened, turned upside down, placed in an special vacuum oven. They are heated to melt and remove the wax, leaving behind a cavity in the shape. The wax removed from the mold can be recycled after proper treatment.
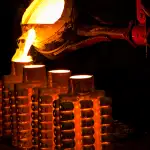
Casting and cooling ⇒
The ceramic mold is preheated to around 1000 – 2000°F (550 – 1100°C) and filled with molten metal, liquid metal flows into the pouring cup, through the central gating system, and into each mold cavity on the tree. Then wait for cooling and solidify
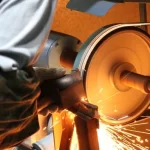
Casting Shell Removal ⇒
Once the casting solidifies, break the ceramic shell first with a Oscillating machine and then by hand, and use angle grinder to cut the individual investment castings from the sprue. Finally remove the excess metal from casting body by grinding.
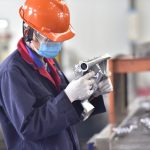
Finishing and Subsequent processing
Sandblasting, grinding, and machining is performed to finish the casting dimensionally. This process allows for high precision and quality in the final product, making it a popular choice in various industries.
Subsequent processing after casting
Customized Investment Casting Machining Service
Precision Investment Casting & Machining Services for Specialized Industries
For manufacturers in high-demand industries—including Medical, Automotive, Aerospace, Elevator, Jewelry, and Optics—investment casting often serves as the foundation for producing intricate metal components. Following the investment casting process, precision machining techniques such as CNC machining, drilling, milling, grinding, and turning ensure tight tolerances and superior surface finishes.
As an ISO 9001-certified and ITAR-registered provider, we specialize in high-precision investment casting and machining services designed to meet and exceed the strictest industry standards. Our state-of-the-art equipment and deep expertise allow us to machine investment cast parts with exceptional accuracy, delivering:
✔ Unmatched Quality – Precision-engineered components with tight tolerances
✔ Rapid Production – Efficient workflows to meet tight deadlines
✔ Cost-Effective Solutions – Optimized processes to reduce waste and expense
Whether you require prototype investment casting or high-volume production, our services are fully customized to your exact specifications. Trust us for precision investment casting and machining that elevates performance and reliability.
Investment Casting Machining Quality & Certifications
- IAF 16949 / ISO 9001:2015 certified
- 99.9% on time delivery and Average 7 days turnaround machining time
- wide range options of machining materials
- Multiple options of machining technology: CNC Machining, Lathing, Drilling, Milling, Grinding and Welding etc.
- Specialized in machining precision casting parts.
Investment Casting CNC Machining Materials
Aluminum | 2024, 5083, 6061, 6063, 7050, 7075, etc. |
Copper Alloy | brass 360, 101 copper, 110 copper, 932 bronze, zinc, etc. |
Titanium Alloy | grade 2, grade 5, etc. |
Stainless Steel | 303, 304, 410, 17-4, 2205 Duplex, 440C, 420, 316, 904L, etc. |
Superalloy | Kovar,Hastelloy,Inconel,monel,etc |
Zinc Alloy | 3#,6#,9# etc., |
Engineering Plastic | POM (Delrin), ABS (Acrylonitrile Butadiene Styrene), HDPE, Nylon, PLA, |
PC (Polycarbonate), PEEK (Polyether Ether Ketone), PMMA (Polymethyl Methacrylate or Acrylic), | |
PP (Polypropylene), PTFE (Polytetrafluoroethylene), etc. | |
Other | Other CNC machining materials: Graphite, VeroClear |
Our Investment Casting Machining Capabilities
- CNC Lathing and Milling Machine
- CNC Swiss Turn by Tsugami
- High Speed Drilling-Tapping Machine
- MAZAK 5 Axis Turning-Milling Machine
- CNC Milling Turning Centers
- Multi Spindle Cam Automatics
- CNC Swiss Turning Machine
- DMU 5 Axis CNC Machine
Investment Casting Inspection Capabilities
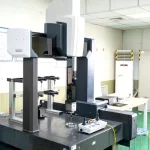
Dimension Tests
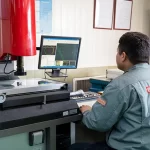
Chemical & Physical Tests
Get a Quote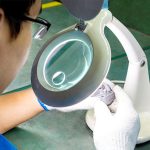
Nondestructive Tests
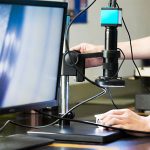
Special Required Tests
Dimentional Tolerance of Investment Castings
Investment Casting Dimensional Tolerance: Definition & Importance
Casting dimensional tolerance defines allowable deviation limits for investment casting measurements during production. Critical factors like precision casting processes, material behavior, and mold stability directly impact these tolerances. Maintaining compliance with dimensional tolerance standards balances quality control and casting production costs - tighter tolerances increase manufacturing precision but may raise expenses by 15-25%. Adhering to scientific casting standards ensures optimal supplier-buyer alignment across aerospace, automotive, and energy sectors.
Investment Casting Standards: GB/T 6414-1999 vs ISO 8062:1994
China's GB/T 6414-1999 (aligned with ISO 8062:1994) governs investment casting dimensional control through:
✅ Unified tolerance benchmarks for sand casting and precision investment casting
✅ 16-tier CT grades (CT1-CT16) ranging from ±0.1mm (CT1) to ±38mm (CT16)
✅ Tolerance selection guidance for:
- High-volume production (CT4-CT8 for automotive investment castings)
- Low-volume batches (CT9-CT12 for prototyping)
This dual-standard framework enables global compatibility for casting process design and quality inspection.
Key Specifications for Investment Casting Tolerance Control
The standard categorizes casting dimensional accuracy by method:
Casting Type | Typical CT Grade | Tolerance Range* |
---|---|---|
Investment Casting | CT4-CT6 | ±0.25mm-±0.8mm |
Die Casting | CT5-CT7 | ±0.4mm-±1.2mm |
Sand Casting | CT8-CT11 | ±1.6mm-±6.5mm |
*For 100mm dimensions
Core coverage includes:
- Basic dimensional tolerances (linear/mismatch allowances)
- Surface finish requirements (Ra 3.2-12.5μm for precision investment castings)
- Machining allowances adjustment protocols
Optimizing Tolerances for Investment Casting Production Scale
Strategic tolerance grade selection depends on batch size:
✅ Mass Production (10,000+ units)
- Recommended: CT4-CT6 (±0.25-0.8mm)
- Achieves <0.5% scrap rate through automated investment casting processes
✅ Small-Batch Production (50-500 units)
- Recommended: CT7-CT9 (±0.8-2.5mm)
- Balances cost-efficiency with ±1.2% dimensional consistency
Tolerance classes for mass-produced rough castings (GB/T6414—1999) (ISO 8062:1994)
Casting Method | Tolerance CT | ||||||||
Casting Material | |||||||||
Cast Steel | Cast Iron | Ductile Iron | Malleable Cast Iron | Copper Alloy | Zinc Alloy | Light Metal Alloy | Nickel Based Alloy | ||
Handmade Sand Casting | 11-14 | 11-14 | 11-14 | 11-14 | 10-13 | 10-13 | 9-12 | 11-14 | |
Machine Moldeling Sand Casting | 8-12 | 8-12 | 8-12 | 8-12 | 8-10 | 8-10 | 7-9 | 8-12 | |
Metal Mold Casting or Low Pressure Casting | 8-10 | 8-10 | 8-10 | 8-10 | 7-9 | 7-9 | |||
Die Casting | 6-8 | 4-6 | 4-7 | ||||||
Investment Casting | Water Glass | 7-9 | 7-9 | 7-9 | 5-8 | 5-8 | 7-9 | ||
silica sol | 4-6 | 4-6 | 4-6 | 4-6 | 4-6 | 4-6 |
Applications of Investment Casting
A Good Investment Casting Manufacturer-Factors to Consider
When choosing an investment casting manufacturer, there are several factors to consider:
5 Key Factors When Choosing an Investment Casting Manufacturer
Selecting the right investment casting supplier is critical for project success. Here are the essential criteria to evaluate:
1. Product Quality Assurance
- Verify the manufacturer’s ability to produce precision investment castings that meet your exact specifications
- Look for certifications like ISO 9001, AS9100 (for aerospace investment casting), or ISO 13485 (for medical investment casting)
- Request material test reports and sample castings
2. Industry-Specific Experience
- Prioritize suppliers with proven expertise in your sector:
- Automotive investment casting (engine components, turbochargers)
- Industrial investment casting (valves, pumps)
- Defense investment casting (armor components)
- Ask for case studies of similar projects
3. Production Capacity & Lead Times
- Evaluate:
- High-volume investment casting capabilities
- Secondary operations (machining, heat treatment)
- Typical lead times for prototype investment casting vs. production runs
- Ensure they can scale with your demand
4. Customer Support & Technical Collaboration
- The best investment casting companies offer:
- Dedicated engineering support
- DFM (Design for Manufacturing) feedback
- Real-time production updates
- Post-delivery technical assistance
5. Cost Competitiveness Without Quality Compromise
- Compare investment casting prices across 3-5 qualified vendors
- Beware of suspiciously low bids – they often indicate:
- Inferior materials
- Lack of process controls
- Hidden fees
Bonus: 3 Questions to Ask Potential Suppliers
- “What’s your scrap/rework rate for [your specific part]?”
- “Can you provide references from clients in our industry?”
- “How do you handle design modifications during production?”
What Clients Said
Hear from Honored Investment Casting Clients
At Sipx, where customer satisfaction is our major priority. Here is what some of our Investment casting customers have said about our products and services.
Chapter 1
Advantages of Investment Casting
Investment Casting: Precision Manufacturing for Complex Components
Investment casting (also known as precision casting or lost-wax casting) enables manufacturers to produce parts with intricate geometries and tight tolerances that are impossible to achieve with conventional casting methods. This versatile metal casting process offers unmatched advantages for demanding applications across multiple industries.
Why Choose Investment Casting?
-
Superior Design Flexibility
- Create complex investment castings with thin walls (down to 0.5mm), internal channels, and detailed features
- Eliminate secondary machining for many components
-
Exceptional Accuracy & Precision
- Achieve dimensional tolerances of ±0.005 in/in (±0.127mm)
- Maintain consistent quality for high-volume investment casting production
-
Premium Surface Finish
- Obtain smooth casting surfaces (125-250 Ra µin) without additional polishing
- Ideal for aesthetic components and fluid flow applications
4. Extensive Material Options
-
- Compatible with high-performance alloys including:
- Stainless steels (17-4PH, 316L)
- Superalloys (Inconel 718, Hastelloy)
- Titanium alloys (Grade 5, Ti6Al4V)
- Compatible with high-performance alloys including:
Key Industry Applications
- Aerospace investment casting: Turbine blades, fuel system components
- Automotive investment casting: Turbocharger housings, transmission parts
- Medical investment casting: Surgical instruments, orthopedic implants
- Industrial investment casting: Valve bodies, pump components
1.1-Design flexibility
Unmatched Design Freedom with Investment Casting
Investment casting (also known as precision casting or lost-wax casting) enables manufacturers to produce components with complex geometries and intricate details that are impossible to achieve through conventional casting methods. This advanced metal casting process gives engineers unprecedented design flexibility to create parts with unique shapes and custom features that meet exact specifications.
Virtually Unlimited Manufacturing Capabilities
The investment casting process imposes almost no restrictions on part structure, size, or complexity, making it suitable for an exceptionally wide range of applications. This versatile manufacturing method can produce:
- High-precision castings with wall thicknesses ranging from 0.5mm to several meters
- Components measuring from a few millimeters to several meters in length
- Parts weighing anywhere between a few grams to hundreds of kilograms
- Complex alloy castings in stainless steel, aluminum, titanium, and superalloys
Optimizing Investment Casting Process Design for Quality Results
Producing high-quality investment castings requires not only advanced casting processes and equipment but also a part structure inherently compatible with precision casting requirements. To ensure casting quality, simplify production workflows, and align designs with investment casting capabilities, the part must demonstrate structural casting process adaptability. This critical performance characteristic—where design meets casting process optimization—is termed the casting process of the part structure.
Key Steps in Investment Casting Part Design
A qualified investment casting design involves three critical phases:
- Functional Design
Prioritize part performance and application requirements. - Casting-Oriented Design Refinement
Simplify geometries using investment casting expertise to minimize:
- Undercuts requiring complex cores
- Non-uniform wall thickness
- Sharp transitions causing stress concentrations
- Metallurgical Design Optimization
- Select casting alloys (stainless steel, aluminum, superalloys) based on:
- Melting characteristics
- Mold material compatibility
- Balance technical requirements with cost-effective casting solutions
- Select casting alloys (stainless steel, aluminum, superalloys) based on:
Structural Review for Casting Process Compliance
When analyzing part structures for investment casting production:
- Primary Foc
- us: Ensure design preserves casting quality and functionality. Avoid oversimplifying structures at the expense of performance.
- Collaborative Problem-Solving: If structural flaws are identified during design reviews, work with the investment casting manufacturer, design team, and end-users to implement revisions that maintain part integrity.
Two-Part Casting Process Evaluation
- Str
uctural Casting Suitability
Verify compliance with investment casting process requirements (draft angles, section thickness, feature accessibility). - Defect Prevention Strategy
Anticipate common casting defects (shrinkage porosity, inclusions) and implement design safeguards such as:- Gradual thickness transitions
- Strategic riser placements
- Controlled solidification patterns
Developing an Effective Investment Casting Plan
Formulate casting process plans by:
- Assessing production capabilities (equipment, workforce expertise)
- Evaluating order quantities (prototype vs. mass production)
- Comparing multiple casting process optimization scenarios
- Aligning with practical foundry capabilities and technical feasibility
Factors Influencing Investment Casting Structure Design
The rationality of investment casting structures depends on:
- Material Properties: Behavior of selected casting alloys during solidification
- Quality Standards: Dimensional tolerances and surface finish requirements
- Production Parameters:
- Casting process method (silica sol vs. ethyl silicate)
- Batch size and lead time constraints
- Automation level of precision casting facilities
1.2-High accuracy and precision
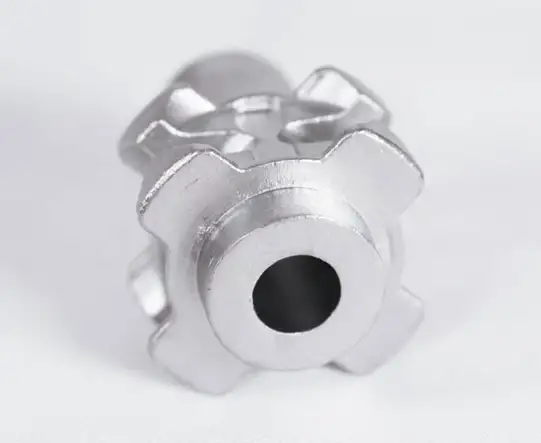
Superior Precision with Investment Casting Technology
Investment casting (also known as precision casting or lost-wax casting) delivers exceptional dimensional accuracy, typically achieving tolerances of ±0.005 in/in (±0.127mm). This level of precision casting ensures final components meet stringent specifications, making it indispensable for mission-critical industries like aerospace investment casting (turbine blades, engine components) and medical investment casting (surgical tools, implantable devices). The process consistently outperforms sand casting and die casting in maintaining tight tolerances while reducing post-processing costs.
Why Investment Casting Outperforms Other Methods
Comparative studies show investment casting achieves industry-leading dimensional control, surpassing alternative casting processes in three key areas:
- Near-Net-Shape Results: Over 90% of investment cast parts require no machining—only light blasting or finishing—saving time and material costs.
- Complex Geometry Retention: Maintains intricate features (thin walls down to 0.5mm, micro-channels) that would deform in other methods.
- Material Versatility: Compatible with high-temperature alloys (Inconel, Titanium) unsuitable for conventional casting.
1.3-Smooth Surface Finish
The investment casting process results in a smooth surface finish that requires little to no additional finishing or polishing. This is ideal for parts that require a high-quality surface finish, such as those used in medical implants or jewelry, Household items, such as cabinet door handles, pot handle casting, casting faucets, robot accessories, etc. If you are looking for a casting method with good rough surface performance. Investment casting is the right choice.
Of course, there are many facts that affect the roughness of investment castings. Let’s take a look at some of the factors that lead to rough casting surfaces and the corresponding improvement measures in detail below.
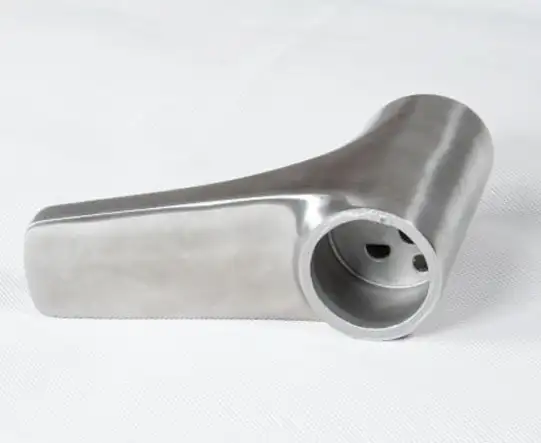
-
Key Factors Affecting Surface Roughness in Investment Casting
When producing precision investment castings, surface finish quality is critical for meeting tight tolerances and functional requirements. Several process variables can lead to rough casting surfaces—here are the most common causes and proven investment casting surface improvement methods:
1. Low Viscosity in Surface Slurry
Problem: Insufficient slurry viscosity creates poor coating adhesion, resulting in rough investment castings.
Solution: Increase viscosity by adjusting the binder-to-refractory ratio and maintaining optimal slurry temperature (30-45 sec Ford Cup #4).2. Delayed Sand Stuccoing Process
Problem: Prolonged wait times before stuccoing allow slurry to partially gel, degrading investment casting surface finish.
Solution:- Train operators to apply stucco within 30-60 seconds after dipping
- Implement process audits to ensure timely sand application
3. Coarse Surface Sand Grit
Problem: Large sand particles (>80-mesh) create texture transfer to castings.
Optimization:- Use 100-120 mesh sand for surface layers
- Balance fineness: Too coarse → Roughness; Too fine → Permeability issues
4. Excessive Sand Drop Height
Problem: High stuccoing distance embeds sand into slurry, worsening casting surface roughness.
Fix: Reduce drop height to <30 cm and use fluidized bed sanders for even distribution.5. Air Bubbles in Slurry
Problem: Entrapped air causes pinholes in shells, leading to defective investment castings.
Correction:- Add defoamers (0.1-0.3% by weight)
- Use vacuum degassing or low-shear mixing
6. Incomplete Refractory Wetting
Problem: Poor slurry homogeneity creates inconsistent investment casting surfaces.
Best Practice:- High-shear mix for 20+ minutes
- Age slurry 24-48 hours for full hydration
Why Surface Finish Matters in Investment Casting
Achieving smooth investment casting surfaces is essential for:
✓ Dimensional accuracy in precision components
✓ Reduced post-machining costs
✓ Improved fatigue resistance in critical applicationsFor industries like aerospace investment casting and medical device investment casting, these optimizations ensure compliance with ISO 9001/AS9100 standards.
1.4-Wide Range of Material Options
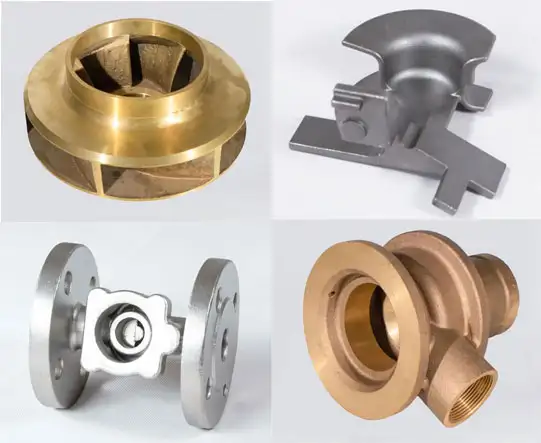
Investment casting can use a wide range of materials, including high-performance alloys, stainless steel, and titanium. This provides designers with the flexibility to choose the best material for their specific application, ensuring the final product meets the required performance and durability standards.
The diversification of investment casting materials has made it widely used in multiple popular industries, including automotive, aerospace, electric, petrochemical, agriculture, medical equipment, shipbuilding, and construction industry, etc
FAQs on Investment Casting Service
Investment casting is a manufacturing process that involves creating a mold, pouring molten metal into the mold, and then removing mold to reveal the finished part. It is different from other casting methods in that it allows for the production of highly complex and intricate parts high precision and accuracy.
A wide range materials can be used in investment casting, including stainless steel, aluminum, copper, brass, and various alloys.-performance materials such as titanium and Inconel can also be used.
Investment casting is used in various industries including aerospace, automotive, medical, military, and jewelry.
When choosing an investment casting manufacturer, it is important to consider factors such as quality of products, experience and expertise, production capacity, customer service and support, price competitiveness.
To get a quote from an investment casting manufacturer, you typically need to provide them with the part design, material requirements and expected production volume.
The typical lead time for investment casting varies depending on the part complexity and production volume, but can range from a weeks to several months.
To ensure the quality of investment cast parts, is important to work with a reputable manufacturer that uses quality control processes and has a track record of producing high-quality.
Common defects in investment casting include porosity, shrinkage, cracks, and surface irregularities.
Investment casting is generally a more expensive manufacturing method compared to casting methods, but it offers benefits such as the ability to produce complex parts with precision and accuracy.
The minimum order quantity for investment casting varies depending on manufacturer and part complexity.
Investment casting manufacturers typically offer post-casting services such as machining, surface finishing, and assembly.
The typical tooling cost for investment casting depends on the part complexity and production volume, but can range from a few thousand to tens of thousands of dollars.
The maximum wall thickness for investment casting depends on the material and part geometry but is typically around 1 inch.
The typical lead time for investment casting varies depending on the part complexity and production volume, but can range from a weeks to several months. The maximum weight limit for investment also depends on the material and part geometry, but can range from a few ounces to several hundred pounds.
Investment casting can be used produce parts with internal cavities using ceramic cores.
The typical surface finish for investment cast parts is around -250 RMS (root mean square) but can be improved additional surface finishing processes.
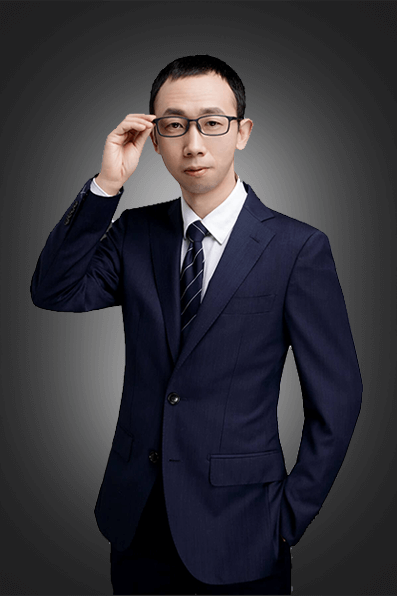
At SipxMach, our goal is to help our customers lower production costs and increase production rates and quality. Interested to see what SipxMach can do for you and your team? Contact us to schedule a tour of our state-of-the-art facility
- Contact: Rubio
- Email: [email protected]
- Microsoft Teams: Rubioli8677 (Sales manager)
- Office Add: No.551, Baosheng Avenue, Huixing Street, Yubei District, Chongqing, China
- Foundry Add: No. 4 Jindi Avenue, Dongcheng Street, Tongliang District, Chongqing