Pump casting manufacturer
Searching for Pump casting manufacturers? Our casting foundry offer precision Pump casting with quick quotation and fast delivery service. Valve casting manufacturing is the process of creating valve components, such as valve bodies, discs, and stems, through the use of casting techniques. This involves pouring molten metal or other materials into a mold to create the desired shape and size of the valve component. Valve casting manufacturing is widely used in the production of valves for a variety of industries, including oil and gas, chemical, water treatment, and power generation. The process allows for the creation of high-quality, durable valve components that can withstand harsh operating conditions and provide reliable performance over an extended period of time.
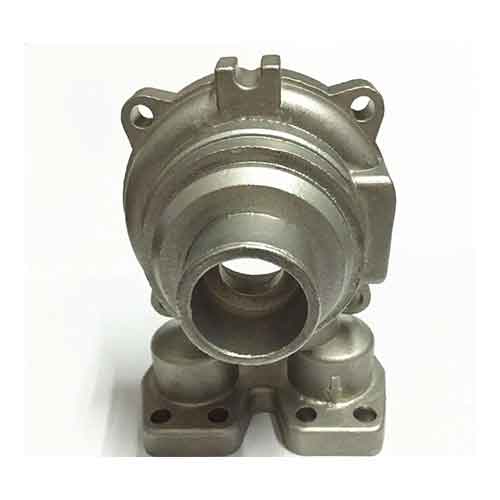
pump shell casting
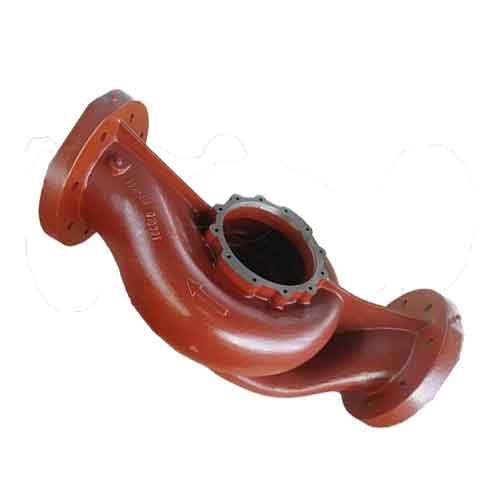
pump shell casting with coating
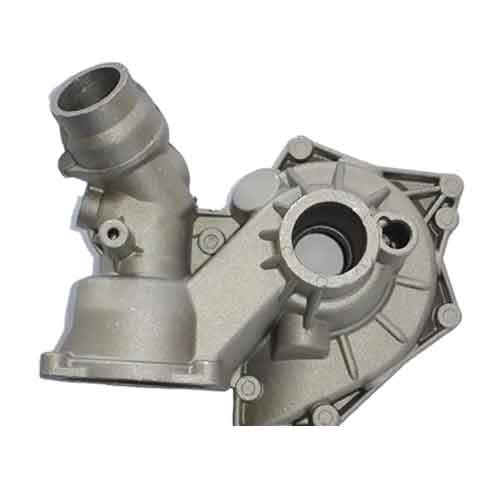
pump casting parts
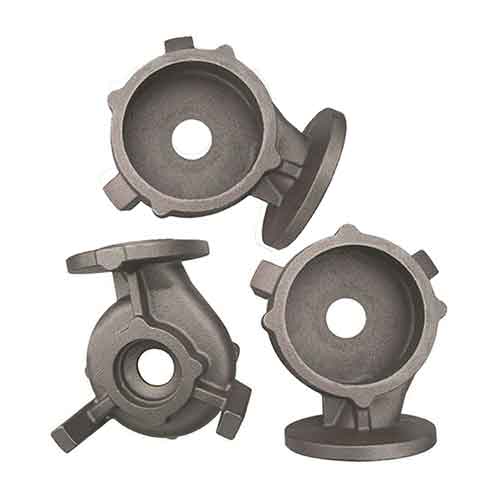
sand casting gray iron pump shell
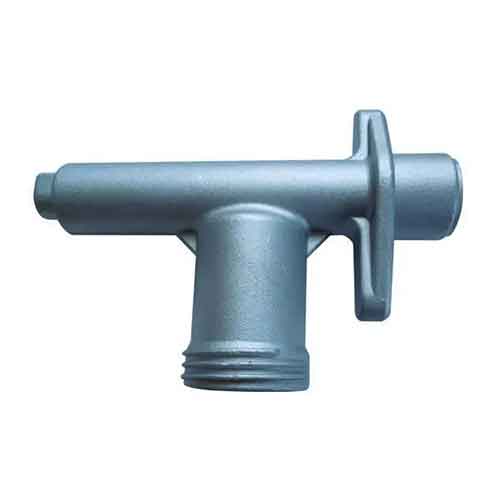
automotive clutch pump castings
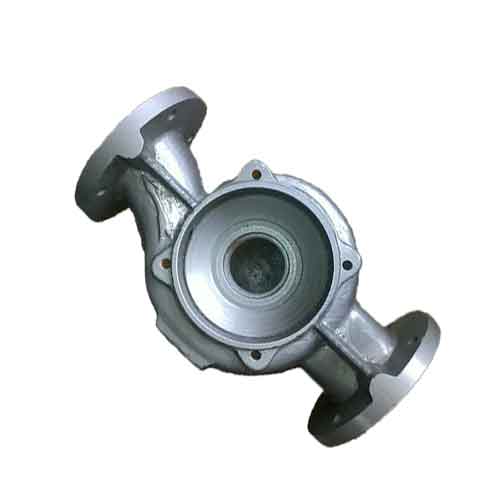
casting vertical fire pump parts
Different casting methods used for pump casting
There are several methods used in the manufacture of pump castings, including sand casting, investment casting, and die casting.
Sand casting is the most common method and involves creating a mold from sand and then pouring molten metal into the mold. Investment casting involves creating a wax model of the component and then coating it with a ceramic material. The ceramic-coated model is then heated, causing the wax to melt away and leaving a ceramic mold that is used to cast the metal component. Die casting involves forcing molten metal under high pressure into a mold cavity.
The type of pump casting method used will depend on the specific requirements of the component being manufactured. Pump castings can be made from a variety of metals, including iron casting, steel casting, aluminum, and bronze, depending on the application and performance requirements. The finished pump casting must meet strict quality standards to ensure that it performs reliably and effectively in its intended application.
Types of materials used for pump casting manufacturer
Pump casting requires materials with high strength, corrosion resistance, and good wear resistance. The selection of materials for Pump casting depends on the application, operating conditions, and the fluid or gas being handled. Some of the commonly used materials for pump casting include:
Materials |
Detail |
Alloy Steel |
Alloy Steel is a popular material choice for pump castings due to its strength and durability. It is also resistant to corrosion and can withstand high temperatures |
Stainless Steel |
Stainless steel is a popular material choice for pump castings, especially in applications where corrosion resistance is important. It is also strong and durable, and has good fluid-carrying capabilities. |
Aluminum |
Aluminum is lightweight, and it offers good corrosion resistance and thermal conductivity. It is often used for pumps that handle water and other low-viscosity fluids. |
Cast iron |
Cast iron is a durable material that is commonly used for pump castings. It is strong, resistant to wear and tear, and has good fluid-carrying capabilities. |
Brass |
Brass is a non-ferrous metal that is widely used for pump castings. It is corrosion-resistant, has good fluid-carrying capabilities, and is easy to machine. |
Bronze |
Bronze is a strong and durable material that is often used for pump impellers and casings. It is resistant to corrosion and wear, and can withstand high temperatures. |
Post processes after pump casting
After casting process, there are several post-processes that may be required to achieve the desired final product. These post-processes include:
- Heat treatment: The pump casting may undergo heat treatment to improve its strength and durability. This process involves heating the casting to a specific temperature and holding it for a certain amount of time to alter its microstructure. This can also improve the casting’s resistance to corrosion and wear.
- Machining: After casting, the pump may require machining to achieve the desired shape, size, and surface finish. Machining operations such as turning, drilling, milling, and grinding can be used.
- Surface preparation: The casting surface may require cleaning or preparation before it can be painted, plated, or coated. Processes such as sandblasting, shot peening, or polishing may be used.
- Nondestructive testing: The pump casting may undergo nondestructive testing such as X-ray, ultrasonic, or magnetic particle inspection to detect any defects, cracks, or porosity.
- Assembly: Once all the processes are completed, the pump casting may be assembled with other components such as shafts, bearings, and seals to form a complete pump system.
- Quality control: The casting may undergo quality control checks to ensure that it meets the required specifications and standards. This may involve measuring dimensions, testing for leaks, and conducting performance tests.
Different industries that use pump castings
Pump casting is a widely used manufacturing process that produces pump components used in various industries. Some of the common applications of pump casting include:
- Agricultural Industry: Pumps are used for irrigation purposes, to pump water from wells, and other agricultural applications.
- Chemical Industry: Pumps are used to transfer and process chemicals in various manufacturing processes.
- Oil and Gas Industry: Pumps are used to extract, transport, and refine oil and gas from the ground.
- Water Treatment Industry: Pumps are used to transport, filter, and treat water in municipal and industrial water treatment plants.
- Mining Industry: Pumps are used for slurry, mine dewatering, tailings disposal, and other mining applications.
- Food Industry: Pumps are used to transfer food and beverage products during production, as well as in bottling and packaging applications.
- Pharmaceutical Industry: Pumps are used to transfer and process various pharmaceutical compounds during production.
- Marine Industry: Pumps are used for ballast water treatment, as well as for various offshore drilling and processing applications.
- Construction Industry: Pumps are used for concrete pumping and dewatering applications on construction sites.
- Power Generation Industry: Pumps are used for cooling and lubrication systems, as well as for fuel transfer and sewage treatment in power plants.
In summary, pump casting is a versatile manufacturing process that produces pump components used in various industries that require high-performance and reliability in severe-service applications.
Investment casting process for pump body
A wax model of the pump body was successfully produced by assembling a water-soluble core and wax model for pump body castings with large external dimensions and complex shapes. The pump body casting was successfully cast by using silica sol technology for shell making, designing a reasonable pouring system, determining a reasonable dewaxing process and pouring process.
Pump products are widely used to transport various fluids. To ensure performance, high requirements are placed on the dimensional accuracy and surface bar longitude of the inner wall flow channel of the pump body, as well as the pressure value and appearance quality of the pump body itself. Due to the limitations of its process characteristics, investment casting generally has a casting weight of only a few grams to a few kilograms. For castings with large dimensions and complex shapes, there are certain difficulties in both pressing wax molds and shell making processes.
Example: A batch of pump bodies (casting blanks) with an external dimension of 515mm × 410 mm, with a mass of 47.85 kg, made of CF8M material, as shown in Figure 1. After careful design and adopting a reasonable process plan, this batch of pump body castings has been successfully produced.
1、 Wax mold production
1.1 Production of urea core
Due to the structural characteristics of the pump body itself, it is impossible to directly press out the inner cavity of the pump body from the mold. According to the actual production, the urea core process is adopted. As the dimensional accuracy and surface roughness of the pump body flow channel are all determined by the urea core, the production requirements of the urea core are strict. Urea and white sugar are mixed in a (mass ratio) of 100:5 and heated to 130-150 ℃. After melting, they are poured into a model with evenly coated turpentine in the inner cavity. After complete cooling, the urea core is taken out for inspection. The urea core is required to be white, with a smooth and defect free surface, and the size is qualified.
1.2 Wax Model Production
The wax pressing temperature is 54-60 ℃, the injection pressure is 0.8-1.0 MPa, the injection time is 50 seconds, and the holding time is 10 minutes. The flange plate is individually waxed and welded for bonding. The wax mold surface and inner cavity surface are required to be smooth, without flow patterns, with the large flange on the side perpendicular to the bottom and parallel to the 12 convex countertops on the opposite side. If necessary, shaping is required.
1.3 Flow injection system design
The casting needs to undergo a pneumatic test, and no defects such as shrinkage or porosity are allowed inside. Considering that the 12 protrusions on the front and the root of the water outlet are the hot spot areas, a supplementary shrinkage riser has been appropriately added above the casting. Two flow injection system schemes were designed based on the structural characteristics of the castin
g.
(1) Option 1 injection method is riser top injection
Adopting a cross shaped die head with assembly
welding, the length is determined by the casting, the width of the runner is 55mm, the thickness of the runner is 50mm, and the size of the flow cup is Φ 30 mm x Φ 90mm × 180 mm.
(2) Option 2 injection method is joint injection
On the basis of Scheme 1, add one side of the sprue and sprue cup at the bottom of the pump body, and connect it to the bottom flange.
2、 Shell making
To ensure the strength of the shell and the surface roughness of the casting, the silica sol process is adopted. The specific process parameters are shown in Tables 1 and 2.
Due to the large volume and uneven wall thickness of the casting, if ordinary dewaxing methods are used for dewaxing, the shell may experience bulging and cracking due to uneven heating. Therefore, it is necessary to improve the dewaxing process to achieve sequential dewaxing.
The specific method is to wrap the pump body shell with three layers of waste newspaper, exposing the riser and runner. This way, the wax mold of the pouring system is melted and flows out first, forming a channel for the flow out of the pump body wax mold, thereby achieving sequential dewaxing. The dewaxing pressure is 0.6-0.75 MPa, the dewaxing time is 25-30 minutes, and the shell condition is good after dewaxing.
Table 1 Coating Preparation | ||||
Coating | Coating type | ratio of liquid to powder/s | Guan’s fluid viscosity | Note |
1-2 layer | Silica sol+zircon powder | 1:3.6 | 36土2 | Zircon powder with a particle size of 320 mesh |
3 layer | Silica sol+coal gangue powder | 1:(1.6-1.8) | 16-19 | The particle size of coal gangue powder is 30-60mesh |
4-7 layer | Silica sol+coal gangue powder | 1:(1.3-1.5) | 13-15 | The particle size of coal gangue powder is 16-30 mesh |
sealing layer | Silica sol+coal gangue powder | 1:(1.1-1.2) | 12-18 |
Table 2 Shell making parameters | |||||
Coating | Sanding type | drying temperature/centigrade | Humidity | drying time | Wind speed (a/s) |
1 layer | 100 mesh Zirconium sand | 24土2 | 50-70 | 8-9 | breezeless |
2 layer | 80 mesh mullite sand | 24土2 | 50-70 | 12-14 | breeze |
3 layer | 30-60 mesh coal gangue sand | 24土2 | 40-60 | 15-16 | 3-5 |
4-7 layer | 16-30mesh coal gangue sand | 24土2 | 30-50 | 16-18 | 6-8 |
sealing layer | 24土2 | 30-50 | 24 | 6-8 |
3、 Shell cultivation and casting
Due to the large volume of the mold shell and the thickness of the casting wall, in order to ensure the quality of the mold shell firing, the firing temperature should be appropriately increased and the insulation time should be extended. The cultivation temperature used is 1080-1100 ℃, and the cultivation time is 1 hour. After adopting scheme 1 for pouring, severe shrinkage and porosity occurred at the hot joint at the root of the casting outlet. The casting quality produced by using Plan 2 is good.
The specific pouring process is as follows: first, use a side gate cup to pour the molten steel to 2/3 of the entire casting, and then use a middle flow cup to fill the molten steel. The shell temperature is greater than 950 ℃, the molten steel pouring temperature is 1620-1630 ℃, and the pouring time is 120 seconds. To prevent shrinkage and loosening, add molten steel and cover the riser with insulation agent within 30 seconds after pouring. During the cooling process of the casting, local water quenching is carried out at the hot joint at the root of the protrusion and outlet.
By designing a reasonable wax mold production process and shell making process, a larger pump body shell can be manufactured. The method of sequential dewaxing was adopted to effectively prevent bulging and cracking of the mold shell. The improved pouring system scheme was adopted, and after cleaning the castings, there were no shrinkage holes or looseness, and there was no obvious deformation. After inspection, the surface quality met the user’s requirements, the size was qualified, and the air pressure test was qualified.
FAQ
- What is pump casting manufacturing?
Pump casting manufacturing is the process of creating metal castings to build pumps, which are used to move fluids, such as water, oil, and gas, from one place to another.
- What materials are used in pump casting manufacturing?
Common materials used include iron, steel, aluminum, brass, and bronze.
- What kind of pumps can be manufactured through pump casting?
Pumps for various applications, such as centrifugal pumps, diaphragm pumps, gear pumps, metering pumps, plunger pumps, and submersible pumps can be manufactured through pump casting.
- What are the advantages of pump casting manufacturing?
The advantages of pump casting manufacturing are its efficiency, ease of production, customization, and cost effectiveness.
- What are the steps involved in pump casting manufacturing?
The steps involved include designing the casting mold, melting the metal, pouring the molten metal into the mold, allowing it to cool and solidify, demolding, finishing, and testing.
- How do I choose a reliable pump casting manufacturer?
Choose a pump casting manufacturer with extensive experience, knowledge, equipment, and resources to meet your specific requirements. It is also important to check their quality standards, certifications, and customer feedback.
- What is the lead time for pump casting manufacture?
The lead time for pump casting manufacture depends on several factors, such as the complexity of the design, material availability, production capacity, and finishing requirements. It usually takes a few weeks to a few months.