What is Lost wax casting?
Lost wax casting (also known as investment casting) is a highly precise metal casting process that produces near-net-shape components with exceptional dimensional accuracy. As one of the oldest metalworking techniques, it dates back thousands of years in China and remains a cornerstone of modern precision casting manufacturing.
The Evolution of Lost Wax Casting Technology
Since the 1990s, Chinese foundry engineers have revolutionized lost wax casting processes by integrating advanced technologies from around the world. These innovations have significantly expanded industrial applications of investment casting, making it a preferred method for industries requiring high-precision metal parts, such as:
- Aerospace (turbine blades, engine components)
- Medical (surgical implants, dental prosthetics)
- Automotive (fuel injection systems, turbochargers)
- Industrial Machinery (pump housings, valve bodies)
Our Expertise in Precision Lost Wax Casting
At Sipx Casting Foundry, we specialize in delivering high-quality investment castings through:
✅ Advanced Process Design
- Optimized wax pattern creation for complex geometries
- Custom ceramic shell molding techniques
- AI-assisted casting simulation for defect prevention
✅ Strict Quality Control
- Dimensional tolerances as tight as ±0.005mm
- X-ray & CT scanning for internal defect detection
- Material testing to ensure superior mechanical properties
✅ Proven Industry Applications
- Over 200+ successful casting projects across multiple sectors
- Case studies demonstrating cost-effective casting solutions
- Continuous R&D to enhance casting efficiency and durability
Why Choose Lost Wax Casting?
Compared to other metal forming processes, investment casting offers:
✔ Minimal machining required (near-net-shape production)
✔ Superior surface finish (reducing post-processing costs)
✔ Wide material compatibility (stainless steel, superalloys, titanium)
Lost wax casting manufacturing processes
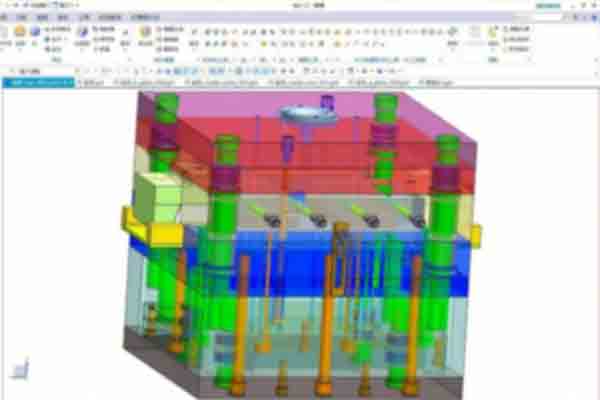
Step 1: Lost wax mold design
According to the requirements of the casting parts drawing to design mold.
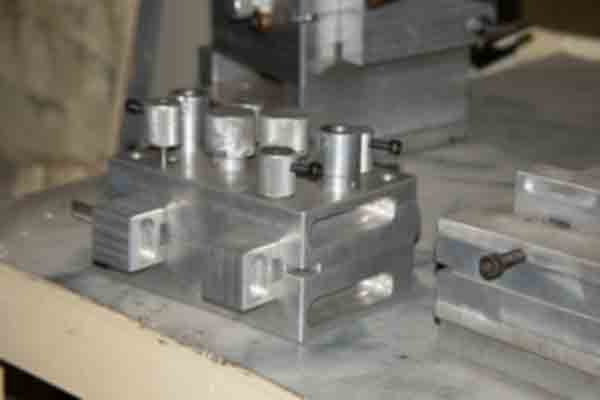
Step2: Manufacturing mold:
According to the mold tooling design drawings to manufacture molds. the mold material normally is iron steel or aluminum.
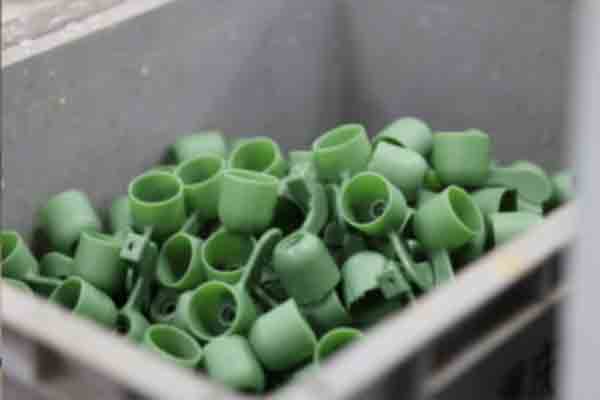
Step3: Manufacturing the lost wax mold
Using a hydraulic wax injection machine or an air-driven wax press, injecting liquid wax into the press to make a wax mold.
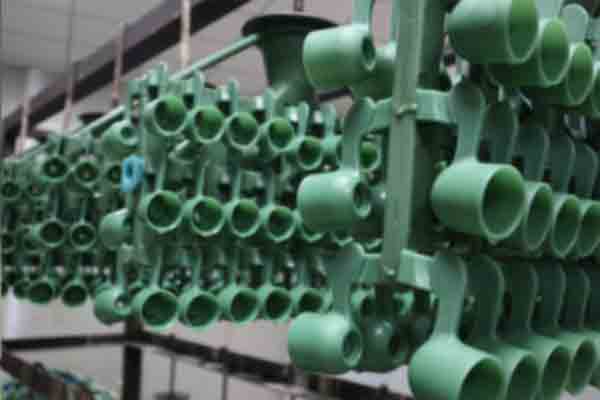
Step4: Wax assembly module
The wax mold is welded or glued to the precast wax stick to form a module
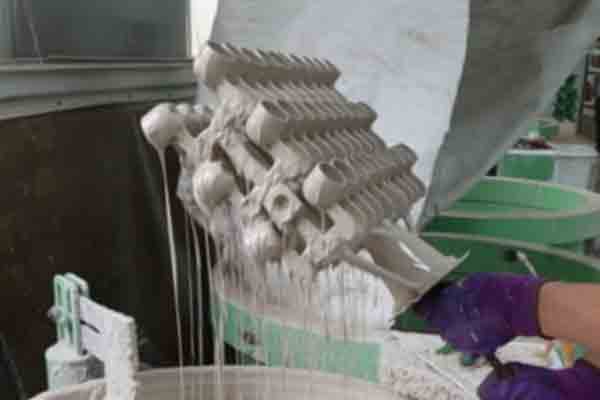
Step5: Degreasing
Immerse the mold in a special degreasing solution to remove the oil and release agent on the surface of the wax mold, so as to increase the adhesion of the wax mold.
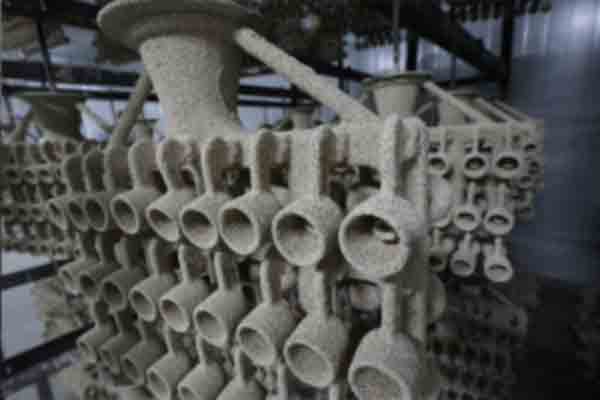
Step6:Manufacturing shell
Apply fire-resistant coating(slurry) on the surface of the module, and sprinkle a layer of sand(zircon sand, corundum sand, silica sand, etc.).
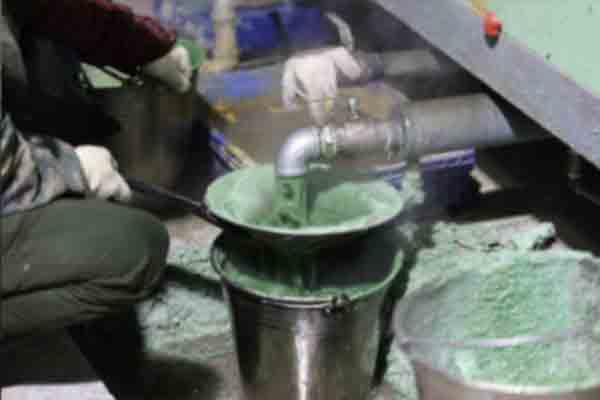
Step7: Lost wax casting
Heating the already made mold shell in steam or hot water, melting all the wax molds to obtain a mold shell with internal cavities.
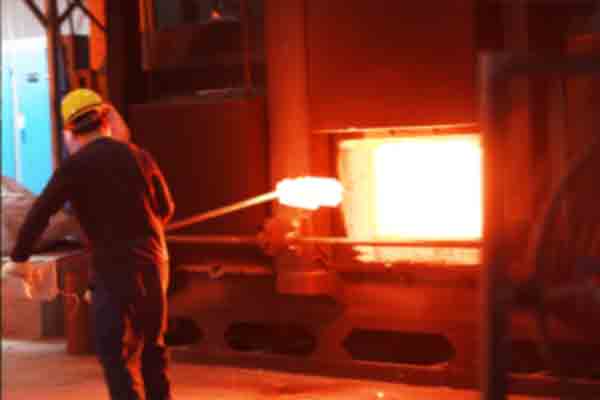
Step8: Shell baking
Placing the shell in a high-temperature oven for high-temperature baking to remove residual wax, various volatile substances and water from the shell.
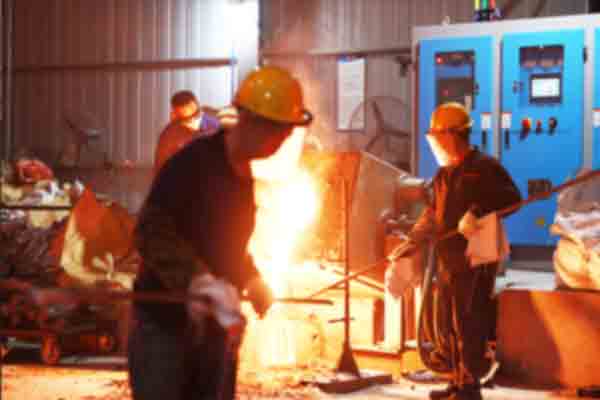
Step9: Liquid metal casting
Pouring qualified high-temperature metal liquid that has been melted with chemical components into a fully baked hot mold shell
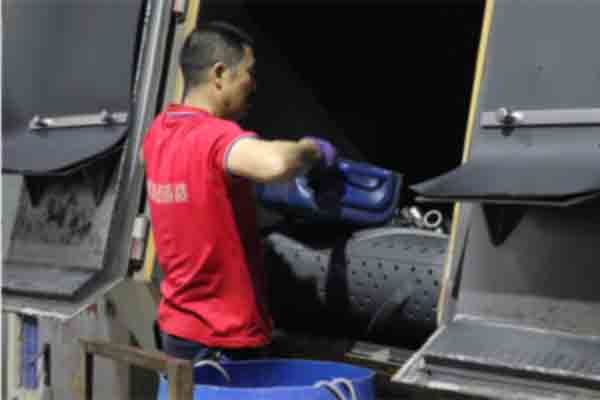
Step10: Deburring and cleaning
deburring with hand tools or virbratory deburring machines, removing sand, cutting the castings after pouring and gating, followed by other cleaning and post-treatment processes.
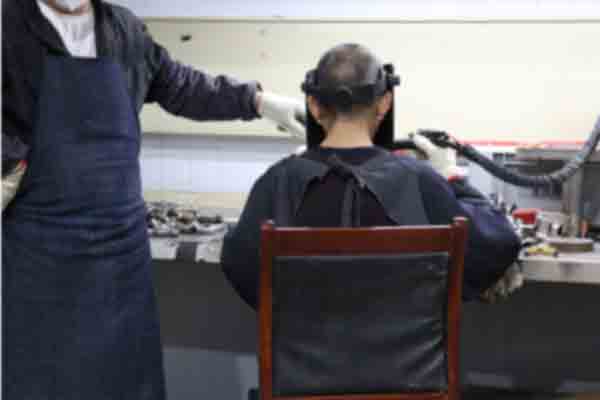
Step11: Inspection
All lost wax casting parts must be checked then could put into warehouses.
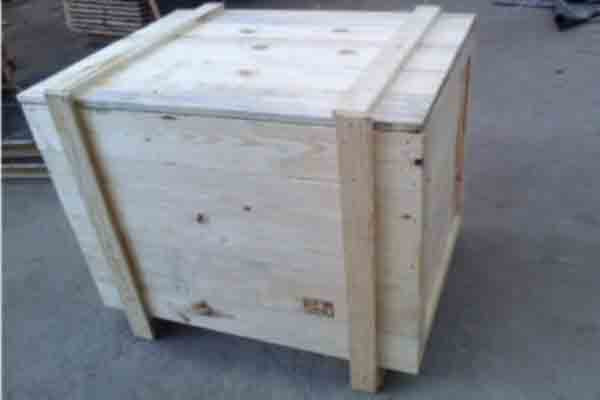
Step12: Packing and transportation
Packed according to client’s needs. Keep safe transportation.
Customized Machining Lost Wax Casting Service
Lost Wax Casting Machining Quality & Certifications
IAF 16949 / ISO 9001:2015 certified
99.9% on time delivery and Average 7 days turnaround machining time
wide range options of machining materials
Multiple options of machining technology: CNC Machining, Lathing, Drilling, Milling, Grinding and Welding etc.
Specialized in machining precision casting parts.
CNC Machining Materials related to lost wax casting service
Aluminum 2024, 5083, 6061, 6063, 7050, 7075, etc.
Copper Alloy brass 360, 101 copper, 110 copper, 932 bronze, zinc, etc.
Titanium Alloy grade 2, grade 5, etc.
Stainless Steel 303, 304, 410, 17-4, 2205 Duplex, 440C, 420, 316, 904L, etc.
Superalloy Kovar,Hastelloy,Inconel,monel,etc
Zinc Alloy 3#,6#,9# etc.,
Engineering Plastic POM (Delrin), ABS (Acrylonitrile Butadiene Styrene), HDPE, Nylon, PLA,
PC (Polycarbonate), PEEK (Polyether Ether Ketone), PMMA (Polymethyl Methacrylate or Acrylic),
PP (Polypropylene), PTFE (Polytetrafluoroethylene), etc.
Other Other CNC machining materials: Graphite, VeroClear
Our Lost Wax Casting Service Machining Capabilities
CNC Lathing and Milling Machine
CNC Swiss Turn by Tsugami
High Speed Drilling-Tapping Machine
MAZAK 5 Axis Turning-Milling Machine
CNC Milling Turning Centers
Multi Spindle Cam Automatics
CNC Swiss Turning Machine
DMU 5 Axis CNC Machine
Inspection Ability about our Lost Wax Casting Service
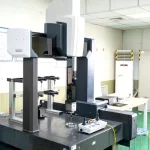
Dimension Tests
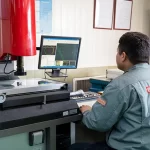
Chemical & Physical Tests
Get a Quote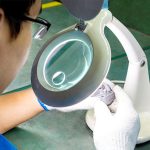
Nondestructive Tests
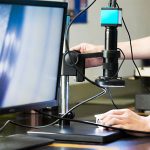
Special Required Tests
Chapter 1
Lost wax casting process has the following advantages and Limitations:
1.1- Lost Wax Casting Advantages
1.1.1-Tolerance
High dimensional accuracy and small surface roughness of lost wax castings. Due to the use of precise and smooth fusible patterns in lost wax casting, it achieves an integral mold shell without parting lines. It also avoids dimensional errors caused by processes like mold release, core removal, and assembly in sand casting. lost wax castings have sharp corners and can achieve dimensional accuracy of CT4~6 grade, with a surface roughness of Rao.8~1.25um. Therefore, castings produced by lost wax casting are closer to the final shape of the parts, reducing the amount of machining required and saving on metal material consumption.
1.1.2-Structure
Lost wax casting, as known as investment casting, is suitable for casting complex and precise structures. It can produce castings that are difficult to produce using other methods, such as various types of turbines, impellers, hollow blades, directionally solidified blades, single crystal blades, etc. It can also cast small components with a wall thickness of 0.5mm, minimum casting hole size of 1mm, weight as small as lg, up to 1000kg, and overall dimensions exceeding 2000mm. Moreover, it allows for the integration of multiple parts into a single casting.
1.1.3-Material
No restrictions on alloy materials. Various alloy materials such as carbon steel, alloy steel, stainless steel, high-temperature alloys, copper alloys, aluminum alloys, magnesium alloys, iron alloys, precious metals, and cast iron can be used in lost wax casting. Especially for alloys that are difficult to machine, lost wax casting is a more suitable process.
1.1.4-Batch Quantity
lost wax casting can be used for both large and small-batch production. Since metal molds are commonly used to produce the lost wax casting patterns, it is suitable for mass production. However, using inexpensive gypsum molds, low melting point alloy molds, or silicone rubber molds (commonly used for art and jewelry casting) can also make it applicable for small batch
1.2-lost wax casting has the following limitations:
It is most suitable for producing medium to small castings with a maximum through-hole diameter of 3-5mm, maximum blind hole diameter of 5mm, minimum casting slot width of 2.5mm, and minimum groove depth of 5mm.
- The production cycle is relatively long.
- The cooling rate of the castings is slow, which can lead to coarse grain structure in the castings and surface decarburization in carbon steel castings.
- Requirements for Mold Materials in Lost wax Casting(1) Melting Point: The melting point and solidification temperature range of the mold material should be moderate, with a melting point generally ranging from 50 to 80° The solidification temperature of the mold material is usually selected between 5 and 10°C to facilitate the preparation of the mold material, mold making, and wax removal processes.
- Thermal Stability: Thermal stability refers to the ability of the mold material to resist softening and deformation as the temperature increases. The thermal stability of wax-based mold materials is often expressed by the softening point. It is the temperature at which the deformation (deflection) of a standard cantilever specimen reaches 2mm after heating and insulation for 2 hours. The softening point of the mold material should generally be at least 10°C higher than the temperature of the mold-making workshop.
- Shrinkage: To ensure that the lost wax casting achieves the required dimensional accuracy, the mold material should have low shrinkage, generally less than 1%. High-quality mold materials can have linear shrinkage rates below 0.5%. A small shrinkage rate corresponds to a small expansion coefficient, which also helps prevent cracking of the shell during wax removal.
- Strength: The mold material should have sufficient strength at room temperature to ensure that the lost wax casting does not deform during the mold-making and shell-making processes.
Chapter 2
Lost Wax Casting Wax Mold
2.1-Requirements of Wax Mold Materials for lost wax Casting
2.1.1-Wax Mold Material Melting Point:
2.1.2-Heat Stability of Wax Mold Materials:
2.1.3-Lost Wax Mold Material Shrinkage Rate:
To ensure the dimensional accuracy of lost wax casting, the mold material must have a low shrinkage rate. Typically, this rate should be less than 1%, with high-quality materials achieving a linear shrinkage rate of below 0.5%. A low shrinkage rate directly correlates with a reduced expansion coefficient, which minimizes the risk of shell cracking during the dewaxing phase. This is crucial for maintaining the integrity of the mold and ensuring the precision of the final cast part. By carefully selecting mold materials with these properties, manufacturers can enhance the overall quality and reliability of their lost wax casting processes.
2.1.4-Wax Mold Strength:
2.1.5- Wax Mold Hardness:
2.1.6-Wax Mold Material Flowability:
The mold material should have good flowability to facilitate filling the mold cavity under pressure, achieving sharp edges, accurate dimensions, and a smooth and polished surface of the lost wax casting. It also facilitates the flow of the mold material out of the shell during dewaxing.
2.1.7- Material Wetting Property:
2.1.8- Ash Content:
2.1.9-Weldability:
2.2-Lost Wax Casting Mold Materials
2.2.1-Wax-based Mold Material
2.2.2-Paraffin Low Molecular Weight Polyethylene Mold Material in lost wax casting
Frequently Asked Questions About Lost Wax Casting
Lost wax casting is a manufacturing process that involves creating a mold, pouring molten metal into the mold, and then removing mold to reveal the finished part. It is different from other casting methods in that it allows for the production of highly complex and intricate parts high precision and accuracy.
A wide range material can be used in lost wax casting, including stainless steel, aluminum, copper, brass, and various alloys-performance materials such as titanium and Inconel can also be used.
Lost wax casting is used in various industries including aerospace, automotive, medical, military, and jewelry.
When choosing a lost wax casting manufacturer, it is important to consider factors such as quality of products, experience and expertise, production capacity, customer service and support, price competitiveness.
To get a quote from a lost wax casting manufacturer, you typically need to provide them with the part design, material requirements and expected production volume.
The typical lead time for lost wax casting varies depending on the part complexity and production volume, but can range from a few weeks to several months.
To ensure the quality of investment cast parts, is important to work with a reputable manufacturer that uses quality control processes and has a track record of producing high-quality.
Common defects in lost wax casting include porosity, shrinkage, cracks, and surface irregularities.
Lost wax casting is generally a more expensive manufacturing method compared to casting methods, but it offers benefits such as the ability to produce complex parts with precision and accuracy.
The minimum order quantity for lost wax casting varies depending on manufacturer and part complexity.
Lost wax casting manufacturers typically offer post-casting services such as machining, surface finishing, and assembly.
The typical tooling cost for lost wax casting depends on the part complexity and production volume, but can range from a few thousand to tens of thousands of dollars.
The maximum wall thickness for lost wax casting depends on the material and part geometry but is typically around 1 inch.
The maximum weight limit for investment also depends on the material and part geometry, but can range from a few ounces to several hundred pounds.
Lost wax casting can be used produce parts with internal cavities using ceramic cores.
The typical surface finish for investment cast parts is around -250 RMS (root mean square) but can be improved additional surface finishing processes.
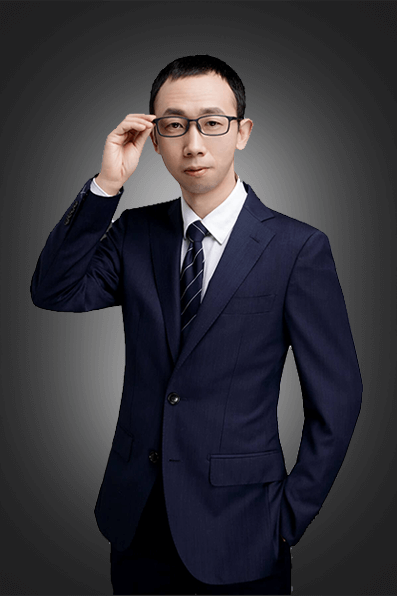
At SipxMach, our goal is to help our customers lower production costs and increase production rates and quality. Interested to see what SipxMach can do for you and your team? Contact us to schedule a tour of our state-of-the-art facility
- Contact: Rubio
- Email: [email protected]
- Microsoft Teams: Rubioli8677 (Sales manager)
- Office Add: No.551, Baosheng Avenue, Huixing Street, Yubei District, Chongqing, China
- Foundry Add: No. 4 Jindi Avenue, Dongcheng Street, Tongliang District, Chongqing