We are not unfamiliar with castings, as they have a long history of application. In ancient times, people used castings to make coins, sacrificial vessels, weapons, tools, and some daily necessities. However, in modern times, castings are mainly used as blanks for machine components or directly as machine components. Casting steel are becoming increasingly common in mechanical products, and their usage is increasing year by year. The shape and variety of castings are also constantly changing. Casting has gradually become an indispensable part of our daily life, and its application can be seen in various occasions such as door handles, locks, and small water pipes, faucets.
Castings have excellent mechanical and physical properties, which can have a comprehensive performance of various strength, hardness, and toughness combinations. They can also have one or more special properties, such as wear resistance, high and low temperature resistance, corrosion resistance, etc.
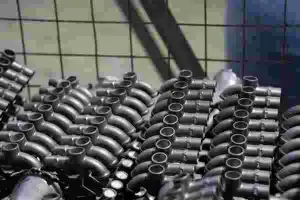
The weight and size range of castings are very wide, with the lightest weighing only a few grams, the heaviest up to 400 tons, the thinnest wall thickness of only 0.5 millimeters, the thickest can exceed 1 meter, and the length can range from a few millimeters to more than ten meters, which can meet the requirements of different industrial sectors.
Compare the differences between stainless steel castings and stainless steel forgings:
- Castings have good wear resistance and shock absorption function, because graphite and pores in the castings are conducive to lubrication and oil storage, so the wear resistance is good. Similarly, due to the presence of graphite and pores, the shock absorption performance of castings is better than that of forged steel.
- Stainless steel castings have good process performance, making them suitable for casting complex or thin-walled parts. In addition, due to the tendency to form chips during cutting, the machinability of castings is better than that of forged stainless steel
- Stainless steel can improve its microstructure and mechanical properties after forging processing. After hot working and deformation by forging method, the cast structure is transformed from coarse dendrites and columnar grains to equiaxed recrystallized structures with finer and uniform sizes due to the deformation and recrystallization of stainless steel. This causes the original segregation, porosity, slag inclusion and other compaction and welding in the steel ingot, making the structure more compact and improving the plasticity and mechanical properties of the metal.
- The mechanical properties of castings are lower than those of forgings of the same material. Forging processing can ensure the continuity of the metal fiber structure, making the fiber structure of the forging consistent with the shape of the forging, and ensuring that the parts have good mechanical properties and long service life. Forgings produced using precision forging, cold extrusion, warm extrusion and other processes are incomparable to castings.
Whether it is castings or stainless steel forgings, they are an indispensable part of mechanical production. In mechanical production, according to the different performance of the product, corresponding castings or forgings are selected. Only by fully playing the role of castings or forgings can perfect mechanical products be produced.