Wall thickness 8mm 57.2kg investment casting part production process
Product description
This product is a sealing component for marine heat exchangers. It is made of CF8M, weighs 57.2kg, and has an overall wall thickness of 8mm. The original process is to stamp and form steel plates and then weld them with plates and pipes. The production efficiency is low, the manufacturing process is complex, and the cost is high. It is relatively high, and requires high flaw detection costs, and the appearance requires surface treatment to achieve good roughness, and the dimensional accuracy cannot meet the requirements of use. The use of investment casting to form one-piece eliminates expensive welding costs, and meets dimensional accuracy requirements, the surface roughness reaches Ra6.3 or above, which can meet the customer’s usage requirements.
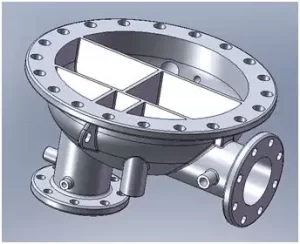
Trial production process
1)Mold making:
The mold is integrally formed and made of forged aluminum 6061. The mold dimensions are approximately: length × width × height = 650mm × 650mm × 420mm. The upper core is cored pneumatically. The mold appearance is shown in the figure below.

2) Module:
The wax injection uses a 20-ton single-station wax injection machine. The wax injection temperature is 52°C, the wax injection pressure is 3.5MPa, the wax injection time is 20 minutes, and the pressure is maintained for 3 minutes. The electric hoist that comes with the wax injection machine is used to assist in starting. The mold and wax mold are water-cooled. The wax parts turnover process, trimming and number of groups are all made by using sponges to lift the bottom. When assembling the tree, it is supported by the tree assembly bracket and bonded with bonding wax. Four auxiliary lifting platforms are used on the top of the mold head. Reinforcement to increase the lifting strength of the entire module. The tree assembly process diagram and process simulation are shown in the figure below:
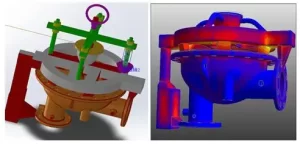
3) Shell making:
The mold shell has 8 layers, namely the surface layer of zircon sand, the transition layer of mullite sand of 50-100 mesh, the back layer of mullite sand of 30-60 mesh (one layer), and the mullite sand of 16-30 mesh (repeat five layers). The drying time of each layer is 24 hours. After the 5th layer of shell making, steel wire mesh is used to reinforce the shell. The traditional shell making operation uses manual direct slurry, rain or boiling sand spreading, but due to the large size of the product , direct manual operation is difficult. In response to this problem, our company has developed a movable shell-making auxiliary trolley for slurry coating. It can be raised and lowered to adjust the height, and can rotate 360 degrees in two directions, which greatly reduces the labor of workers. Strength. In addition, the blind cabin inside the mold shell is filled with dry sand after 4 layers to avoid poor drying of the inner cavity and solve the difficulty of cleaning the mold shell during the cleaning process. The drying method is suspended drying in a directional drying chamber to facilitate the inside of the mold shell drying of the cavity. As shown below:
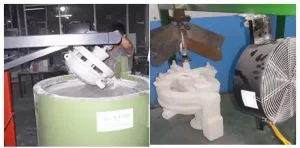
Dewaxing uses electric steam dewaxing kettle, one piece per furnace, and the dewaxing time is 15 minutes
4) Shell roasting:
The shell is roasted using a gas roasting furnace with a roasting temperature of 1120°C and a roasting time of 1.5 hours. Due to the heavy shell, it is not easy to install and pour using traditional fork shells. During trial production, we designed a shell roasting tool (composed of 50*50mm Welded from steel plates), it is loaded into the furnace together with the mold shell to facilitate the picking and placing of the mold shell. Shell loading and unloading are performed using a manual forklift (the teeth of the forklift are pre-wrapped with refractory cotton to avoid deformation caused by high temperature heat). See below:
5) Pouring:
The pouring process uses subcontracting. Since the overall wall thickness of the product is only 8mm, in order to ensure that the metal is completely filled with the mold, the pouring temperature is 1680°C and poured quickly. There is no under pouring problem in the casting after pouring. The cast after pouring is shown in the picture below.
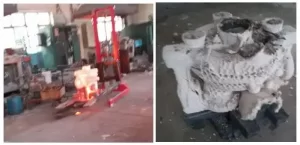
6) Cleaning:
The post-processing process is a normal process flow – manual vibration shell ->shot blasting ->cutting ->grinding ->shot blasting ->welding repair ->heat treatment ->shot blasting ->acid washing ->shot blasting ->passivation ->machining ->pressure testing ->inspection ->warehousing ->packaging. Due to the heavy weight of the castings, the grinding process is assisted by self-made electric gourd grinding, and the turnover of products in the cleaning workshop is entirely carried out by turnover vehicles.
Summary
The use of silica sol technology for precision casting can produce castings weighing more than 50kg, with dimensional accuracy meeting the CT6 level requirements of GB/T6414-1999 and surface roughness reaching Ra6.3. Special auxiliary tools are used during the shell making process, auxiliary tools are used for shell baking, and lifting tools are used during the cleaning process, reducing labor intensity for workers. The overall casting of welded products reduces production costs. The product has completed trial production of castings and can preliminarily meet the requirements for mass production.