what is Volute? Volute is a spiral or scroll-like ornament that is commonly found in architecture and design. It is often used to decorate the capital of a column or as an embellishment on a staircase balustrade. The term “volute” comes from the Latin word “voluta,” which means “scroll.” We usually choose casting as the prior method to make volute. Sipx casting foundry supplies China volute casting parts all over the world.
Volute casting manufacturer
As an established China-based casting specialist, Chongqing Sipx Machinery excels in precision volute casting production. Our engineering team leverages extensive industry expertise to deliver technically advanced volute casting solutions, ensuring optimal performance for demanding applications.
Equipped with automated foundry systems and rigorous quality controls, we guarantee high-integrity volute castings with efficient production timelines. Our commitment to end-to-end service includes collaborative design support and material compliance verification. Partner with us for reliable volute casting manufacturing that prioritizes dimensional accuracy and longevity. Contact our China team today to discuss project specifications and volume requirements.
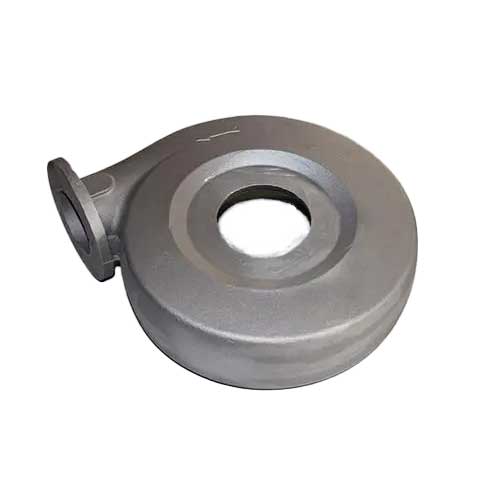
Volute lost wax casting
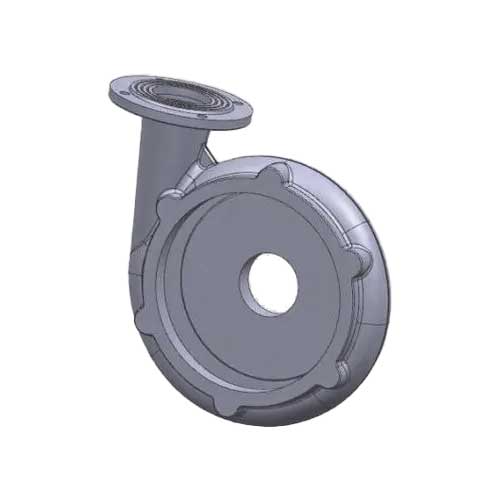
Volute investment casting
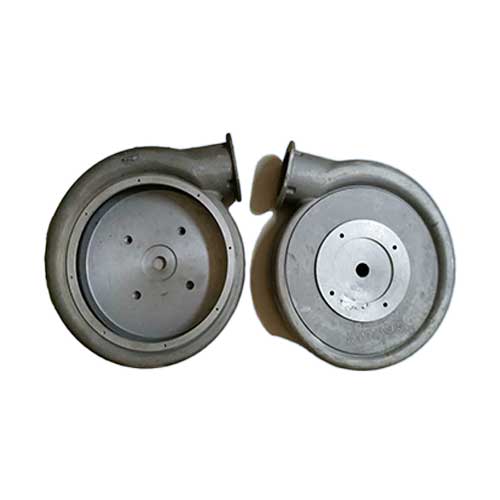
Volute casting parts
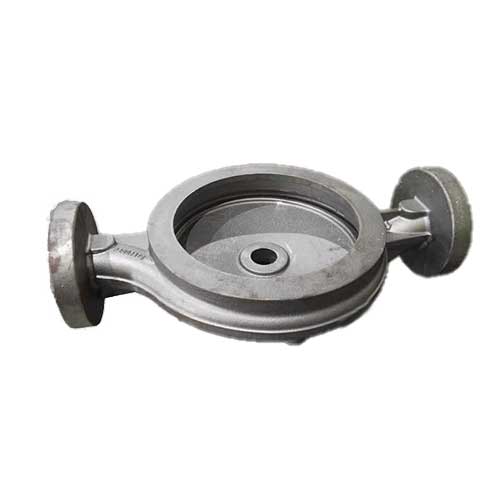
Volute box casting
The manufacturing methods of the volute
The volute casting is a critical centrifugal pump component engineered to convert radial flow into axial flow. Manufacturing methods vary significantly based on application requirements and performance targets, with casting being the predominant solution for complex hydraulic profiles.
At Chongqing Sipx Machinery, we produce volute castings in diverse materials including cast iron, ductile steel, bronze alloys, and aluminum. Our China foundry utilizes precision mold design and controlled metal pouring processes to achieve near-net-shape components. This approach delivers superior cost-efficiency compared to alternative fabrication techniques, particularly for medium-to-high volume production.
While CNC machining may serve for prototype development, it presents limitations in material utilization rates and per-unit costs for batch manufacturing. As a China-based specialist in volute casting service, we recommend investment casting or sand casting for optimal production scalability. Contact us to validate the most technically viable manufacturing strategy for your specific pump requirements.
Centrifugal casting stands as the industry-preferred method for manufacturing volute castings. This process utilizes high-speed rotational velocity during molten metal pouring, forcing material against mold walls to form precise hydraulic geometries. At Chongqing Sipx Machinery, our China-based facilities employ this technique specifically for complex volute casting production.
The centrifugal casting advantage for volute castings manifests in superior metallurgical properties: minimal porosity, controlled grain structure, and enhanced pressure containment capabilities. While alternative methods like investment casting or sand casting service certain applications, they typically deliver lower dimensional consistency compared to centrifugal processing – particularly for large-scale pump components requiring strict hydraulic tolerances.
As a specialized China foundry, we validate each volute casting through non-destructive testing to ensure structural integrity meets international standards. Our technical team provides material selection guidance and flow optimization service to match operational requirements. For volute projects demanding maximum fatigue resistance and leak-proof performance, centrifugal casting remains the technically optimal solution. Contact us for production feasibility analysis based on your pump specifications.
Commonly used material for volute casting
The volute material for a pump can vary depending on the application and preferences of the manufacturer. Some common materials used for casting volutes include:
- Cast iron: This is a popular choice for iron casting manufacturers to make volutes due to its strength, durability, and cost-effectiveness. Cast iron volutes are suitable for a wide range of applications and can resist corrosion and wear.
- Stainless steel: This is another popular material for volutes that require a high level of corrosion resistance. Stainless steel volutes are often used in environments that expose the pump to acidic or salty liquids.
- Bronze: Bronze volutes are typically used when a pump needs to handle corrosive liquids, such as seawater. Bronze is an alloy of copper, tin, and sometimes other metals, and it offers good corrosion resistance and strength.
- Aluminum: Aluminum volutes are often used in smaller, lightweight pumps. Aluminum is lightweight, durable, and resistant to corrosion, making it a good choice for some applications
Designing casting technology for volute castings
This volute casting project features QT500-7 ductile iron components characterized by complex geometries, substantial dimensions (exceeding 1800mm diameter), and controlled wall thickness. Engineered for high-pressure fluid systems, these volute castings demand exceptional impact resistance and thermal stability to withstand operational stresses and impurity-laden media, necessitating rigorous metallurgical control throughout production.
Our China foundry specialists designed the volute casting process with precision:
• Mid-parting mold configuration accommodating structural complexity
• Semi-closed side gating system with horizontal pouring orientation
• Wet sand mechanical molding ensuring dimensional stability
Critical parameters including pouring temperature (1420-1460°C) and gating ratios were optimized through simulation to prevent turbulence defects. This systematic approach guarantees structural integrity for large-scale volute castings.
To eliminate potential defects like micro-cracks, we implement:
-
100% ultrasonic testing (UT) per EN 12680-3 standards
-
High-temperature annealing (920°C ±10°C) for stress relief
-
Ferritization treatment enhancing ductility
The smelting process combines scrap steel with controlled carburization, followed by ladle-based nodularization and trough-inoculation techniques. With shakeout completed at 4916 seconds, each volute casting undergoes shot blasting and defect-free verification before heat treatment – demonstrating our comprehensive quality service from China.
- Review of castings structure and spindle craftsmanship
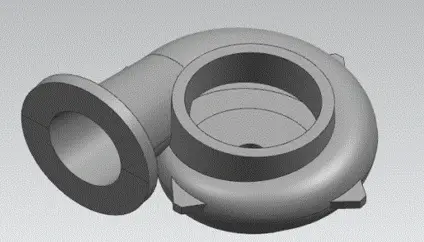
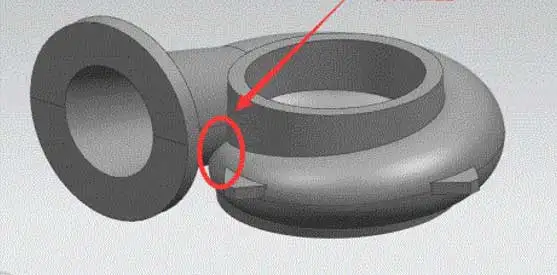
When designing a process, the analysis and summary mainly need to synthesize the following aspects:
Based on the theory and practical experience of alloy solidification, taking into account the above factors and the current volute casting part material QT500-7, the casting adopts an injection pouring system with end face (machining surface).
The specific position shown in the following figure (Figure 3.1) is the pouring surface.
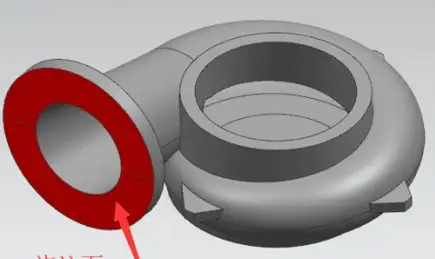
(1) It is best to ensure that all or most of the workpieces are in the same half shape
(2) The determination of the number of parting surfaces needs to adhere to the principle of minimizing the amount possible
(3) It is best not to choose a surface when confirming the parting surface, but to use a flat parting surface
(4) When determining the parting surface in real time, it is necessary to simultaneously consider the issues of core placement, box assembly, and inspection of cavity size
(5) Do not make the sand box too high
Due to the fact that the volute part has an upper and lower half cavity structure, which is similar to a symmetrical structure, the maximum cross-section of the part is used as the parting surface. In this way, the mold can be lifted without the use of active blocks or sand cores, in order to smoothly lift, lower, and fill the mold. As shown in Figure 3.1, select the equal parameter part of the curved shell as the parting surface:
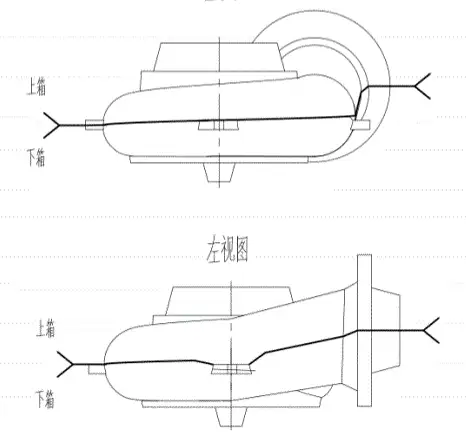
FAQ
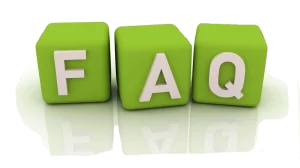
Volute casting is a method of casting a part with a curved, spiral shape. It is used primarily in the production of centrifugal pumps and other rotary machines.
Volute casting involves pouring molten metal into a mold that has the shape of the desired part. The mold is designed to create a cavity that will be filled by the molten metal, forming the volute shape. The mold is then removed, leaving behind a solid metal part.
Volute casting can be challenging to achieve with certain materials, as some alloys may require special casting techniques or equipment. It is also limited in terms of the size and weight of parts that can be produced.
Volute casting is unique in that it creates a spiral shape that is difficult to achieve with other types of casting, such as sand casting or investment casting. It is also typically used for the production of specific types of parts, such as those used in centrifugal pumps.
Volute casting can be done with a wide range of materials, including various types of steel, iron, and non-ferrous alloys.
Volute casting allows for the production of complex shapes, such as spiral volutes, with high precision and accuracy. It is also an efficient and cost-effective method of producing parts with a consistent quality.
Volute casting is used primarily in the production of centrifugal pumps and other rotary machines. It is also used in the manufacturing of some types of turbines and compressors.
We meet the ISO8062(GB/T6414) CT4-CT8 of Nominal dimension (mm) Linear dimension tolerance
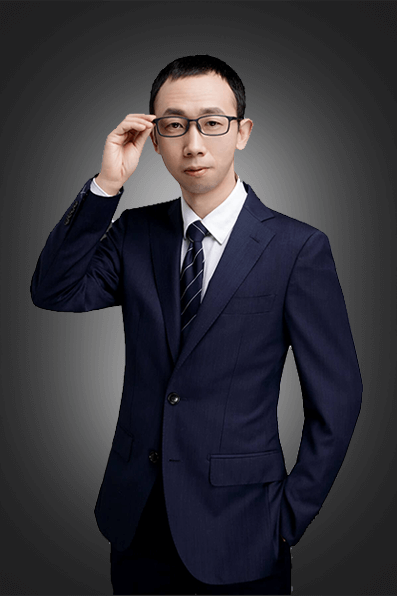
At SipxMach, our goal is to help our customers lower production costs and increase production rates and quality. Interested to see what SipxMach can do for you and your team? Contact us to schedule a tour of our state-of-the-art facility
- Contact: Rubio
- Email: [email protected]
- Microsoft Teams: Rubioli8677 (Sales manager)
- Office Add: No.551, Baosheng Avenue, Huixing Street, Yubei District, Chongqing, China
- Foundry Add: No. 4 Jindi Avenue, Dongcheng Street, Tongliang District, Chongqing