Machined Casting parts
Sipx Iron casting foundry offers the full range of machining services, which includes turning, milling, grinding, drilling and inspection.
Get a Quote
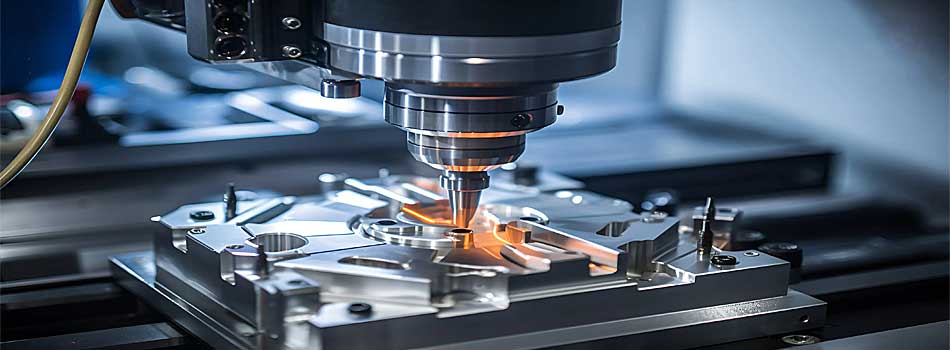
Machined Casting parts can meet the complicated or precision requests for casting parts.The process to cut or remove material from a casting part in order to make the dimensions of the part more accurate is called the machined casting process. Machining after casting also helps to remove an unnecessary portion from a casting part.Once any fettling or heat treatment has been completed and before any finishing processes like anodising or painting, machining takes place. The machining is conducted by computer numerical control (CNC). Specialist computers are programmed in order to guide the machining tools and shape the component accordingly.
Several casting methods, including die casting, investment casting, or sand casting, can be employed to produce the initial castings. Nevertheless, each of these casting methods usually has its own disadvantages, for instance, a rough surface finish or the incapability of creating certain design features.
Product quality can be enhanced and missing design elements can be added with the help of CNC machining. One or more machining processes, such as CNC milling, turning, drilling, milling, or grinding, can be utilized to assist in the creation of high-quality finished products.
Subsequent processing after casting
For manufacturers in some industries, including but not limited to Medical, Automotive, Aerospace, Elevator, Jewelry, and Optic, their products usually request custom Machining, such as CNC machining, drilling, milling, grinding and lathing even after precision casting. we have great experience and equipment to precisely machine tight-tolerance casting parts and components. We offer customized Machining service with ISO 9001 certified and ITAR registered to exceed rigorous standards and unique demands, all while ensuring rapid production, top-notch quality, and cost efficiency.
Aluminum | 2024, 5083, 6061, 6063, 7050, 7075, etc. |
Copper Alloy | brass 360, 101 copper, 110 copper, 932 bronze, zinc, etc. |
Titanium Alloy | grade 2, grade 5, etc. |
Stainless Steel | 303, 304, 410, 17-4, 2205 Duplex, 440C, 420, 316, 904L, etc. |
Superalloy | Kovar,Hastelloy,Inconel,monel,etc |
Zinc Alloy | 3#,6#,9# etc., |
Engineering Plastic | POM (Delrin), ABS (Acrylonitrile Butadiene Styrene), HDPE, Nylon, PLA, |
PC (Polycarbonate), PEEK (Polyether Ether Ketone), PMMA (Polymethyl Methacrylate or Acrylic), | |
PP (Polypropylene), PTFE (Polytetrafluoroethylene), etc. | |
Other | Other CNC machining materials: Graphite, VeroClear |
It is difficult to maintain appropriate tolerances in complex castings, and machining castings can help maintain this. This process is carried out immediately after heat treatment, but before surface treatment such as painting or anodizing. Modern technology uses computer numerical control or CNC machining of castings. There are various types of machining and casting processes, such as:
Machined casting with turning, the blank casting parts rotates and the cutter remains still. The common machine for turning is the lathe machine. This process helps in machining castings from inside and outside. any unwanted material can be removed from the inside and outside of the casting to produce turned bores (holes) and diameters to close tolerances, with a high standard of finish. Carbide or ceramic cutting tools are used to create a smooth finish on the casting. These tools have good wearability, with long life and repeatability.
This type of machining after casting is done to tap or drill holes in a casting part using the drill bit. The primary machine for drilling is the drill press but lathe machines and milling machines are also capable of drilling. Screws on machined casting are usually applied by drilling.
The milling process encompasses four components: the milling machine, cutter, fixture, and workpiece. It is a cutting process in which the cutter on the milling machine rotates to remove unwanted parts from the workpiece. The workpiece is firmly secured on the fixture. Traditionally, turning and milling were carried out separately. However, there are now machines that can perform both operations simultaneously. This not only reduces set – up and tooling times but also cuts costs. Many machined casting parts applied milling process.
Surface grinding is employed to achieve a precise flat finish. The component is fastened onto a magnetic plate or, in the case of non – ferrous castings, a holding fixture. The outer edges of the castings are ground using a carborundum grinding wheel that rotates at a high speed to produce the desired finish. Of cause, most of the casting parts use simple grinding to meet a smooth surface requirement.
Broaching is a machining process used to create or refine a shape with high precision. A broach is a toothed cutting tool. It is pushed or pulled across the surface of the workpiece to remove material in a series of successive cuts. Each tooth on the broach is slightly larger in height than the previous one. As the broach moves along the workpiece, it gradually cuts material to the desired shape and size. For example, if you want to create a keyway (a slot for a key) in a shaft, a broach can be used to cut the keyway with accurate dimensions.
The machining of castings has two primary benefits:
1-Adding detail features and removing extra as-cast material.
2-Improving precision and surface finish.
3-Saving cost.
To better understand why these benefits are so important, let’s explore the applications relevant to each one.
The parts that have just taken out of the mold are called “blank castings” or “As-cast”. They have not been machined, sandblasted, or subjected to other precision machining.
These parts typically have excess material from the gating system, parting lines, and any risers or vents included in the casting design. Then, the foundry must use simple cutting tools to remove unnecessary excess materials. If multiple parts are cast in one mold to improve efficiency, workers must cut them separately.
More intensive CNC machining must be used to produce parts with higher quality requirements to meet product design and eliminate parting lines.
This can remove casting signs and significantly improve the quality of the finished product.
Another key factor in using machining to modify rough castings is the addition of features that cannot be effectively produced using casting. For example, threaded holes.
Even if castings do not require additional machining features and can easily remove excess material, precision CNC machining is an important step in obtaining high-quality parts.
Compared to other casting methods, investment casting and die-casting have better surface smoothness, so they may only require a small amount of machining or polishing to remove parting lines.
However, if castings must have a smooth surface finish, then machining castings becomes crucial for parts produced by sand casting.
Another fundamental reason for machined castings is to improve the accuracy and precision of parts with strict tolerance limitations.
Numerical control machine tools can achieve higher precision than casting.
Manufacturers who need to produce a large number of identical parts can use casting methods to save costs, and then use CNC machining to meet tolerance requirements.
But to achieve this, designers must consider machining allowances during the casting stage.
For machined casting parts, engineers must incorporate machining allowances into the mold design so that the castings have sufficient material for precision machining.
For example, imagine that your finished part has a small protrusion with a very small tolerance. If the mold design has a feature with the same size as the protrusion, any shrinkage or porosity will make that feature smaller than expected. If you need machining to improve the surface finish or refine the shape of the protrusion, engineers will be forced to remove more material.
Adding machining allowances in the part design will slightly increase the size of any blank casting or part features that manufacturers will complete through CNC machining. These allowances help manufacturers consistently meet tolerance requirements, reduce rejected parts, and significantly reduce machining time.
Having amassed many years of casting experience, equipped with top-notch equipment and providing tailored manufacturing solutions, you can rely on us to help you reach the finish line, regardless of whether you possess a time-tested component or are currently in the development stage.