As an iron casting manufacturer, iron casting is a manufacturing process that involves pouring molten iron into a mold to produce a solid metal component. It is one of the oldest and most common casting processes used today. Iron casting is used in various industries, including automotive, aerospace, construction, and agriculture, due to its strength, durability, and ability to withstand high temperatures. There are two main types of iron casting: gray iron casting and ductile iron casting. Gray iron casting is used for applications that require good machinability and wear resistance, while ductile iron casting is used in applications that require high strength and toughness. Iron casting is a versatile and cost-effective way to produce complex metal components with a high degree of accuracy and precision. Many casting parts use iron as their priority, such as volute casting, pump casting, valve casting and pulley casting, etc.
What is ani ron casting manufacturer, and what do they do?
An iron casting manufacturer is a company that specializes in the production and supply of iron castings to various industries. Iron casting suppliers have the expertise and equipment to produce iron castings of various shapes and sizes, using different types of iron alloys, such as gray iron, ductile iron, and alloyed iron.
The main responsibilities of an iron casting manufacturer include: Design and engineering, Patternmaking, Casting, Machining and finishing, Quality control.
Overall, iron casting suppliers play a critical role in the manufacturing industry by providing high-quality iron castings that are used in various applications, from automotive and aerospace to construction and agriculture.
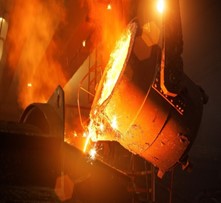
What methods are commonly used for Iron casting?
There are several methods that can be used for Iron casting in an iron casting manufacturer. Some of the most common methods include sand casting, and investment (lost-wax) casting, Gravity die casting manufacturer. Other methods and variations of these methods may also be used, depending on the specific requirements of the project.
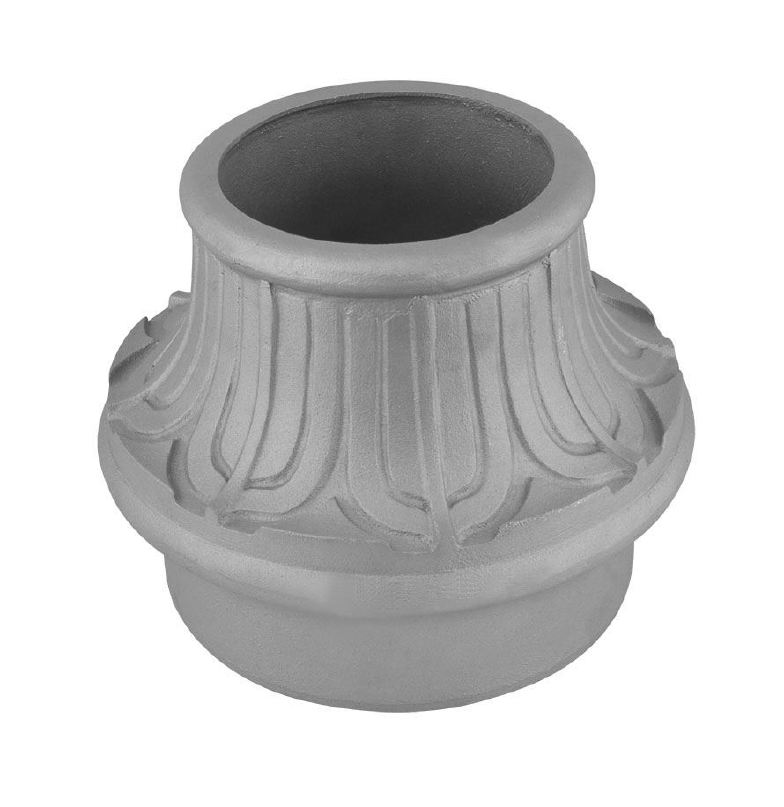
Sand Casting Iron casting manufacturer
Get a Quote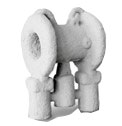
Investment Casting Iron casting manufacturer
Get a Quote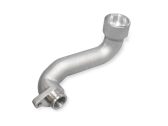
Gravity Casting Iron casting manufacturer
Get a QuoteIron casting manufacturer serves
Iron casting manufacturer serves a wide range of industries and applications. Some common industries that rely on iron casting manufacturers include:
-
Automotive Industry: Iron castings are used in the manufacturing of engine blocks, cylinder heads, transmission cases, and other components for vehicles.
-
Machinery and Equipment Manufacturing: Iron castings are utilized in the production of industrial machinery, agricultural equipment, construction machinery, and various types of heavy equipment.
-
Infrastructure and Construction: Iron castings are employed in the construction of bridges, pipelines, water and sewage systems, and other infrastructure projects.
-
Energy and Power Generation: Iron castings are essential in the manufacturing of components for power generation equipment, including turbines, generators, and other heavy-duty machinery.
-
Rail and Transportation: Iron castings are used in the production of railway components, such as railcar frames, brake systems, and other structural parts.
-
Oil and Gas Industry: Iron castings are utilized in the manufacturing of equipment for oil and gas exploration, production, and processing, including pumps, valve casting manufacturer and drilling components.
-
Mining and Minerals Processing: Iron castings play a vital role in the mining industry by being used in the production of equipment for mineral extraction, processing, and handling.
These are just a few examples of the industries that benefit from the services of an iron casting manufacturer. The versatility and strength of iron castings make them essential components in a wide variety of industrial applications.
Advantages of iron casting over other manufacturer methods
Here are some advantages of iron casting and a brief explanation:
- High Strength: Iron casting is known for its high strength and durability, making it suitable for use in heavy-duty applications.
- Versatility: Iron casting can be used to produce a wide range of complex shapes and sizes, making it a versatile manufacturing process.
- Cost-effective: Iron casting is a cost-effective manufacturing process, as it can produce large quantities of components at a lower cost compared to other manufacturing processes.
- Good machinability: Iron casting is easy to machine and can be finished to a high level of precision, making it suitable for use in precision components.
- Heat resistance: Iron casting has good heat resistance, making it suitable for use in applications that involve high temperatures or thermal shock.
- Corrosion resistance: Iron casting can be treated to improve its corrosion resistance, making it suitable for use in harsh environments.
- Sound damping: Iron casting has good sound damping properties, making it suitable for use in applications that require noise reduction.
Overall, iron casting is a versatile and cost-effective manufacturing process that produces high-strength components with good machinability and resistance to heat and corrosion.
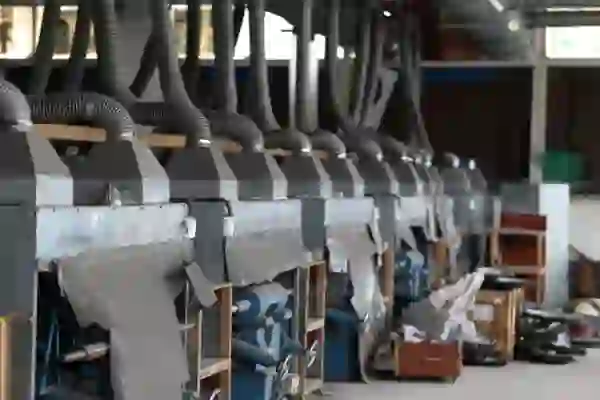
Materials commonly used in casting Iron
There are many iron material brands that are suitable for casting in an iron casting manufacturer, depending on the specific application and requirements. Some of the most common brands used in iron casting include:
Gray iron |
Gray iron is the most commonly used material in iron casting. It is known for its high strength, excellent castability, and good machinability. |
Ductile iron |
Ductile iron is also known as nodular or spheroidal graphite iron. It has excellent tensile strength, good ductility, and high impact resistance. |
White iron |
White iron is a hard, brittle material with high wear resistance. It is commonly used in applications that require high wear resistance, such as mining and construction equipment. |
Malleable iron |
Malleable iron is a ductile material that can be easily shaped and formed. It has good strength and toughness, making it suitable for use in automotive and construction applications. |
Alloy iron |
Alloy iron is a material that is modified with alloying elements such as nickel, chromium, and molybdenum. It has improved mechanical properties such as higher strength and wear resistance. |
Compacted graphite iron |
Compacted graphite iron is a material that has a graphite structure that is intermediate between gray iron and ductile iron. It has high strength, improved thermal conductivity, and good damping properties. |
These listed materials offer a range of properties that can be tailored to specific applications, making iron casting a versatile manufacturing process.
Measures taken by iron casting manufacturer to prevent sand inclusion defects
According to the formation mechanism of sand inclusions, the occurrence of sand inclusions can be prevented from the following aspects:
(1) The correct selection and preparation of molding sand is the main measure to prevent sand inclusion in iron casting manufacturers. If quartz feldspar sand with a small coefficient of thermal expansion is selected as the original sand. Major castings use special sand with low thermal expansion coefficient, no phase change, high thermal diffusion rate, and high thermal storage coefficient as the raw sand. Select raw sand with dispersed particle size (preferably distributed on five adjacent sieves).
Choosing bentonite with high hot wet tensile strength and low hot compression stress, increasing the amount of bentonite added, can improve the anti sand inclusion ability of molding sand. Adding coal powder, heavy oil, wood chips, etc. to the molding sand can reduce thermal stress; Minimize the moisture content of the molding sand as much as possible to ensure the mixing time; The mixed sand, after being evenly mixed and loosened, has a good effect on maintaining stable sand performance and preventing sand inclusion.
(2) In terms of casting technology, avoid pouring large flat surfaces in a horizontal position: the iron casting manufacturer’s pouring system should be able to allow the metal liquid to smoothly enter the mold cavity, and the internal runners should be evenly distributed to prevent local overheating; Increase the blocking area of the sprue appropriately to quickly seal the surface of the baked mold; Reduce the pouring temperature appropriately.
The iron casting manufacturer uses high-strength molds such as sodium silicate sand, limestone sodium silicate sand, resin sand, etc., which can effectively prevent sand inclusion.
The shape requires that the compactness of the molding sand should be uniform, avoiding local hardening or looseness; In areas prone to sand inclusion such as the upper surface and near the pouring channel, more air holes should be drilled to reduce gas pressure, and local reinforcement should be carried out by inserting nails; Dry the surface of the sand mold to improve surface strength.
(3) In terms of casting structure, try to avoid large flat surfaces and ensure that the casting angles are appropriate. The ability of different shaped cavities to resist sand inclusion varies, with concave shapes having the best resistance, followed by flat shapes, and convex shapes having the worst resistance. When conducting process design, iron casting manufacturers should take necessary measures for convex shaped cavities to prevent sand inclusion.
FAQ for iron casting manufacturer
Here are a few frequently asked questions related to iron casting services:
Iron casting is a manufacturing process that involves pouring molten iron into a mold to produce a specific shape or component. The molten iron is allowed to cool and solidify, and the resulting cast part is then finished and machined to the desired specifications.
Advantages of iron casting include high strength, versatility, cost-effectiveness, good machinability, heat resistance, corrosion resistance, and sound damping properties.
Gray iron is a brittle material with a gray color, while ductile iron is a more ductile material with a nodular or spheroidal graphite structure. Ductile iron has higher tensile strength and impact resistance than gray iron.
The lead time for iron casting can vary depending on the complexity of the component, the size of the production run, and the availability of raw materials. Typically, lead times for iron casting can range from a few weeks to several months.
Common materials used in iron casting include gray iron, ductile iron, white iron, malleable iron, alloy iron, and compacted graphite iron.
Industries that benefit from iron casting include automotive, construction, agriculture, aerospace, energy, mining, and marine.
The maximum size of a component that can be produced through iron casting depends on various factors such as the capacity of the equipment and the complexity of the shape. Typically, iron casting can produce components ranging in size from a few ounces to several tons.