As a professional iron casting manufacturer in China, we specialize in this time-honored metal forming process that transforms molten iron into durable components through precision mold casting. Our foundry provides comprehensive iron casting services for global clients across automotive, aerospace, construction, and agricultural industries – leveraging iron’s exceptional strength, heat resistance, and longevity.
We produce two primary types of industrial castings:
Gray iron casting: Ideal for applications demanding superior machinability and wear resistance
Ductile iron casting: Engineered for projects requiring enhanced strength and impact toughness
As a trusted iron casting supplier, our China-based facility utilizes advanced techniques to manufacture complex components with remarkable dimensional accuracy, including:
• Volute castings for pumping systems
• Precision pump castings
• Industrial valve castings
• Heavy-duty pulley castings
Our iron casting solutions combine centuries-old metallurgical knowledge with modern manufacturing excellence, delivering cost-effective components that meet the most demanding specifications. Whether you need standard or custom cast iron parts, our team ensures optimal performance and reliability.
As an iron casting manufacturer, and what do we do?
As a professional iron casting manufacturer in China, our foundry specializes in producing high-quality cast iron components for global industries. We offer comprehensive iron casting services, manufacturing durable parts in various specifications using premium alloys including gray iron, ductile iron, and specialized alloyed iron. Our expertise as a reliable iron casting supplier enables us to deliver precision components for diverse industrial applications.
Our iron casting production process encompasses five key stages: innovative design and engineering, precision patternmaking, advanced casting techniques, meticulous machining and finishing, plus rigorous quality control. As a leading China-based iron casting foundry, we play a vital role in supplying critical components to major sectors including automotive manufacturing, aerospace engineering, construction equipment, and agricultural machinery.
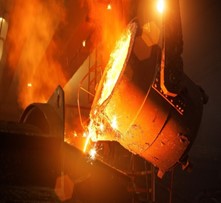
What methods are commonly used for Iron casting?
There are several methods that can be used for Iron casting in an iron casting manufacturer. Some of the most common methods include sand casting, and investment (lost-wax) casting, Gravity die casting manufacturer. Other methods and variations of these methods may also be used, depending on the specific requirements of the project.
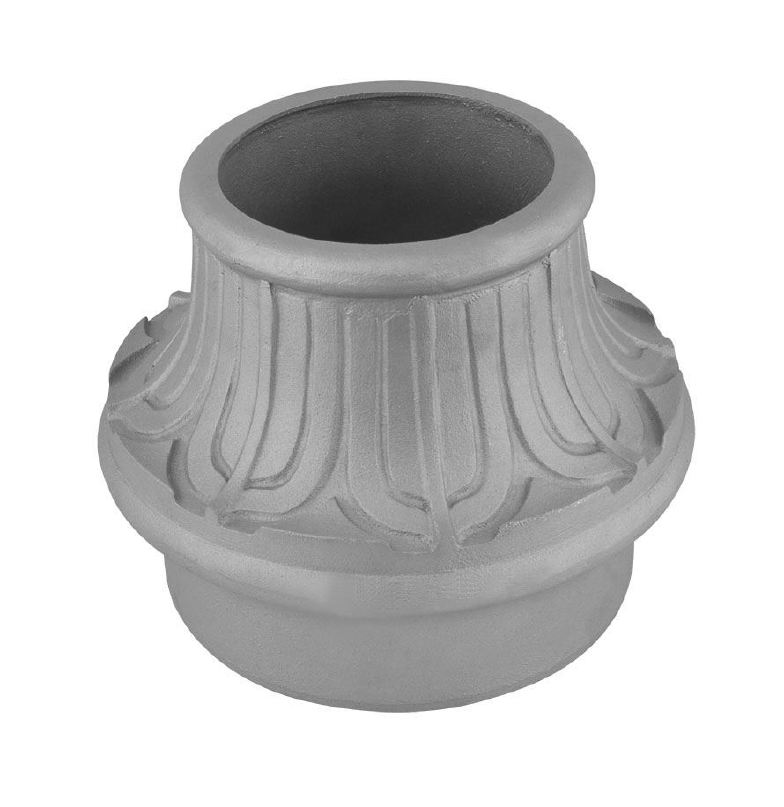
Sand Casting Iron casting manufacturer
Get a Quote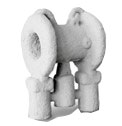
Investment Casting Iron casting manufacturer
Get a Quote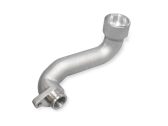
Gravity Casting Iron casting manufacturer
Get a QuoteIron casting manufacturer serves
As a leading iron casting manufacturer in China, our foundry provides premium iron casting services to numerous industries worldwide. The exceptional durability and cost – effectiveness of our cast iron components make them indispensable across multiple sectors:
- Automotive Industry: Our iron castings are widely used in manufacturing critical vehicle components including engine blocks, cylinder heads, and transmission cases for global automotive suppliers. These castings, with their sturdy construction and reliable performance, ensure the proper functioning of automotive engines and transmission systems. The high precision and quality of our iron castings help enhance the overall performance and longevity of vehicles, enabling them to withstand the demanding conditions of daily driving and long – term use.
- Machinery & Equipment: We supply high – quality iron castings for industrial machinery, agricultural equipment, and construction machinery production. Our castings serve as essential components in various machinery, such as the housings and frames for industrial equipment, the parts for agricultural machinery like tractors and harvesters, and the structural components for construction machinery such as excavators and bulldozers. The excellent wear – resistance and strength of these castings ensure the stable operation of machinery in harsh working environments, reducing downtime and maintenance costs for our customers.
- Infrastructure Projects: As a trusted iron casting supplier, we provide durable components for bridges, pipelines, and water systems construction. The iron castings we offer for bridges, such as bridge piers and brackets, are capable of withstanding heavy loads and long – term exposure to outdoor weather conditions. For pipelines and water systems, our castings, like pipeline supports and water pump housings, exhibit superior corrosion – resistance and sealing performance, ensuring the safe and efficient transportation of water and other resources.
- Energy Sector: Our foundry produces precision iron castings for power generation equipment like turbines and generators. These precision castings are crucial for the core components of power generation equipment. They ensure the high – efficiency operation of turbines and generators, helping power plants achieve stable electricity generation and transmission. The high – precision and high – quality castings we provide meet the stringent requirements of the energy sector for equipment performance and reliability.
- Rail Transportation: Railway manufacturers rely on our iron casting solutions for railcar frames and brake systems. Our iron castings for railcar frames provide strong support and stability, ensuring the safe operation of railcars during high – speed travel and heavy – load transportation. In the brake systems, the castings we supply, such as brake discs and brake calipers, offer reliable braking performance and heat – dissipation capabilities, effectively ensuring the safe stopping of trains.
- Oil & Gas: We specialize in valve casting manufacturing and supply critical components for drilling equipment and processing systems. Our valve castings, with their excellent sealing and pressure – resistance properties, ensure the safe and efficient operation of oil and gas pipelines and processing equipment. The iron castings for drilling equipment, such as drill bit holders and drill pipe connectors, are capable of withstanding the high – intensity wear and tear during drilling operations, providing strong support for oil and gas exploration and extraction.
- Mining Operations: Our iron castings are essential for mineral extraction and processing machinery. In mineral extraction equipment, such as crushers and grinding mills, our castings serve as key components like grinding balls and grinding mill liners. They are highly wear – resistant, enabling them to efficiently handle the crushing and grinding of minerals. In processing machinery, our iron castings, such as pump housings and pipeline components, ensure the smooth transportation and processing of mineral slurries, meeting the needs of the mining industry for efficient production.
As an experienced iron casting manufacturer in China, we continue to expand our capabilities to meet the evolving needs of these industries, delivering superior cast iron solutions with exceptional strength and reliability.
Advantages of iron casting over other manufacturer methods
-
High Strength and Durability: Iron casting is renowned for its exceptional strength and durability. As a trusted supplier in China, we produce iron castings that can withstand immense pressure and heavy loads, making them ideal for use in demanding applications such as industrial machinery, construction equipment, and automotive components. Our high – strength iron castings ensure long – term reliability and reduce the frequency of replacements, offering significant cost – savings for our customers.
-
Versatility in Shapes and Sizes: One of the remarkable features of iron casting is its versatility. Our foundry in China has mastered the process of creating a wide range of complex shapes and sizes to meet the specific requirements of different industries. Whether you need intricate automotive engine parts, massive construction machinery components, or delicate precision – engineered pieces for the energy sector, we can produce high – quality iron castings with accuracy and efficiency.
-
Cost – effectiveness: Iron casting is a highly cost – effective manufacturing process, especially when producing large quantities of components. As a professional iron casting manufacturer in China, we optimize our production processes to minimize costs without compromising on quality. By choosing our services, you can benefit from competitive pricing and significant economies of scale, making iron castings an attractive option for businesses looking to reduce production costs while maintaining high – quality standards.
-
Good Machinability: Iron castings produced by our foundry in China offer excellent machinability. They can be easily machined to achieve precise dimensions and tight tolerances, making them suitable for applications that require precision components. This quality ensures that our iron castings can be further processed and integrated into complex assemblies with ease, meeting the specific requirements of your manufacturing processes.
-
Heat Resistance: Our iron castings exhibit superior heat resistance, making them suitable for use in high – temperature environments or applications that involve thermal shock. This property is particularly valuable in industries such as energy generation, where components like turbine parts and heat – exchanger components must withstand extreme temperatures. By choosing our heat – resistant iron castings, you can enhance the performance and longevity of your equipment in challenging thermal conditions.
-
Corrosion Resistance: We specialize in producing iron castings with enhanced corrosion resistance. Through advanced treatment processes, our foundry in China can improve the corrosion resistance of iron castings, making them suitable for use in harsh environments such as those found in the oil & gas, mining, and marine industries. This feature ensures that our iron castings can maintain their integrity and performance even when exposed to corrosive elements, reducing maintenance costs and downtime for our customers.
-
Sound Damping Properties: Iron castings possess excellent sound damping properties, making them ideal for applications where noise reduction is a priority. Our foundry in China produces iron castings that can effectively absorb and reduce noise vibrations, creating a quieter operating environment. This benefit is particularly advantageous in industries such as automotive and machinery manufacturing, where reducing noise levels is essential for improving workplace safety and product quality.
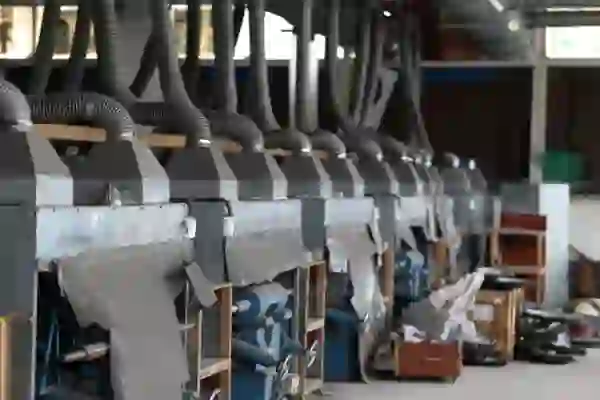
Materials commonly used in casting Iron
There are many iron material brands that are suitable for casting in an iron casting manufacturer, depending on the specific application and requirements. Some of the most common brands used in iron casting include:
Gray iron |
Gray iron is the most commonly used material in iron casting. It is known for its high strength, excellent castability, and good machinability. |
Ductile iron |
Ductile iron is also known as nodular or spheroidal graphite iron. It has excellent tensile strength, good ductility, and high impact resistance. |
White iron |
White iron is a hard, brittle material with high wear resistance. It is commonly used in applications that require high wear resistance, such as mining and construction equipment. |
Malleable iron |
Malleable iron is a ductile material that can be easily shaped and formed. It has good strength and toughness, making it suitable for use in automotive and construction applications. |
Alloy iron |
Alloy iron is a material that is modified with alloying elements such as nickel, chromium, and molybdenum. It has improved mechanical properties such as higher strength and wear resistance. |
Compacted graphite iron |
Compacted graphite iron is a material that has a graphite structure that is intermediate between gray iron and ductile iron. It has high strength, improved thermal conductivity, and good damping properties. |
These listed materials offer a range of properties that can be tailored to specific applications, making iron casting a versatile manufacturing process.
Measures taken by iron casting manufacturer to prevent sand inclusion defects
According to the formation mechanism of sand inclusions, the occurrence of sand inclusions can be prevented from the following aspects:
(1) The correct selection and preparation of molding sand is the main measure to prevent sand inclusion in iron casting manufacturers. If quartz feldspar sand with a small coefficient of thermal expansion is selected as the original sand. Major castings use special sand with low thermal expansion coefficient, no phase change, high thermal diffusion rate, and high thermal storage coefficient as the raw sand. Select raw sand with dispersed particle size (preferably distributed on five adjacent sieves).
Choosing bentonite with high hot wet tensile strength and low hot compression stress, increasing the amount of bentonite added, can improve the anti sand inclusion ability of molding sand. Adding coal powder, heavy oil, wood chips, etc. to the molding sand can reduce thermal stress; Minimize the moisture content of the molding sand as much as possible to ensure the mixing time; The mixed sand, after being evenly mixed and loosened, has a good effect on maintaining stable sand performance and preventing sand inclusion.
(2) In terms of casting technology, avoid pouring large flat surfaces in a horizontal position: the iron casting manufacturer’s pouring system should be able to allow the metal liquid to smoothly enter the mold cavity, and the internal runners should be evenly distributed to prevent local overheating; Increase the blocking area of the sprue appropriately to quickly seal the surface of the baked mold; Reduce the pouring temperature appropriately.
The iron casting manufacturer uses high-strength molds such as sodium silicate sand, limestone sodium silicate sand, resin sand, etc., which can effectively prevent sand inclusion.
The shape requires that the compactness of the molding sand should be uniform, avoiding local hardening or looseness; In areas prone to sand inclusion such as the upper surface and near the pouring channel, more air holes should be drilled to reduce gas pressure, and local reinforcement should be carried out by inserting nails; Dry the surface of the sand mold to improve surface strength.
(3) In terms of casting structure, try to avoid large flat surfaces and ensure that the casting angles are appropriate. The ability of different shaped cavities to resist sand inclusion varies, with concave shapes having the best resistance, followed by flat shapes, and convex shapes having the worst resistance. When conducting process design, iron casting manufacturers should take necessary measures for convex shaped cavities to prevent sand inclusion.
FAQ for iron casting manufacturer
Here are a few frequently asked questions related to iron casting services:
Iron casting is a manufacturing process that involves pouring molten iron into a mold to produce a specific shape or component. The molten iron is allowed to cool and solidify, and the resulting cast part is then finished and machined to the desired specifications.
Advantages of iron casting include high strength, versatility, cost-effectiveness, good machinability, heat resistance, corrosion resistance, and sound damping properties.
Gray iron is a brittle material with a gray color, while ductile iron is a more ductile material with a nodular or spheroidal graphite structure. Ductile iron has higher tensile strength and impact resistance than gray iron.
The lead time for iron casting can vary depending on the complexity of the component, the size of the production run, and the availability of raw materials. Typically, lead times for iron casting can range from a few weeks to several months.
Common materials used in iron casting include gray iron, ductile iron, white iron, malleable iron, alloy iron, and compacted graphite iron.
Industries that benefit from iron casting include automotive, construction, agriculture, aerospace, energy, mining, and marine.
The maximum size of a component that can be produced through iron casting depends on various factors such as the capacity of the equipment and the complexity of the shape. Typically, iron casting can produce components ranging in size from a few ounces to several tons.
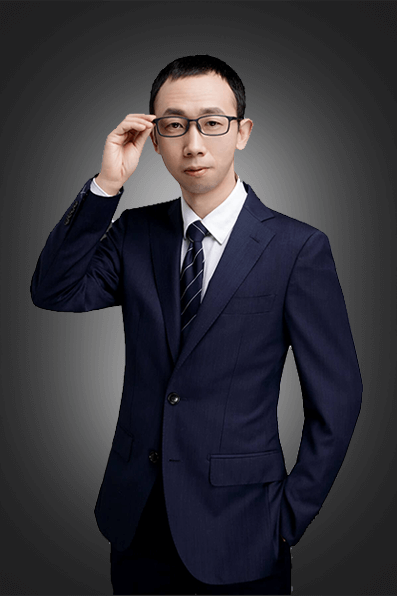
At SipxMach, our goal is to help our customers lower production costs and increase production rates and quality. Interested to see what SipxMach can do for you and your team? Contact us to schedule a tour of our state-of-the-art facility
- Contact: Rubio
- Email: [email protected]
- Microsoft Teams: Rubioli8677 (Sales manager)
- Office Add: No.551, Baosheng Avenue, Huixing Street, Yubei District, Chongqing, China
- Foundry Add: No. 4 Jindi Avenue, Dongcheng Street, Tongliang District, Chongqing