Impeller casting
An impeller casting is a precision-engineered rotating component that enhances fluid pressure, flow rate, and velocity. As a professional China-based impeller casting manufacturer, Chongqing Sipx Machinery produces high-performance impellers featuring optimized vanes or blades that rotate within casings to propel fluids efficiently. These critical components serve diverse applications including pumps, turbines, and compressors, with each impeller casting customized to meet specific system requirements. Our foundry specializes in investment casting technology to deliver superior impeller casting solutions as a reliable global supplier, offering comprehensive service from design to production.
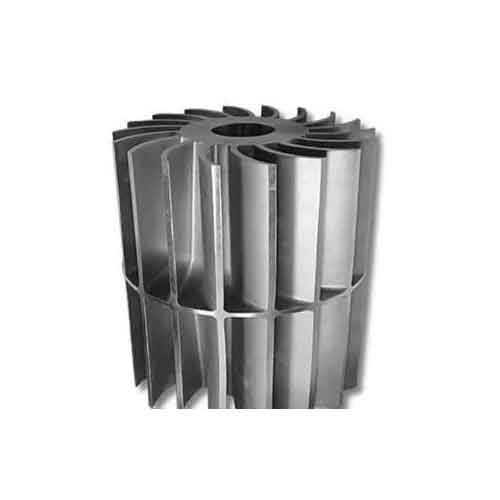
Vacuum pump impeller
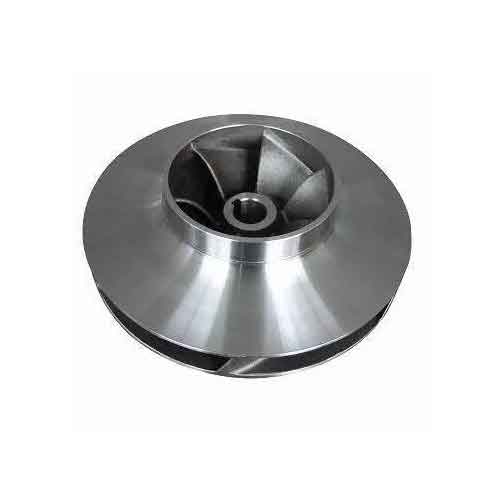
Water pump impeller
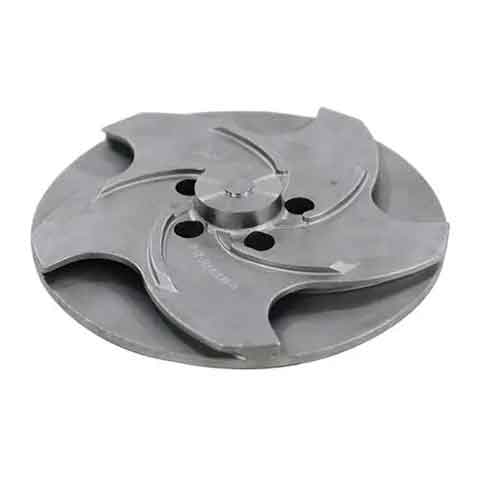
Pump stainless steel impeller
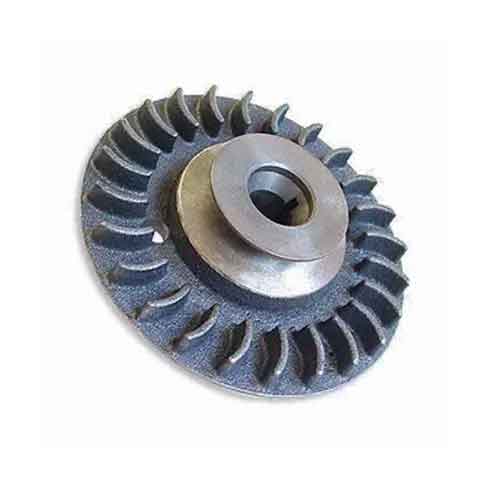
Fan wheel impeller
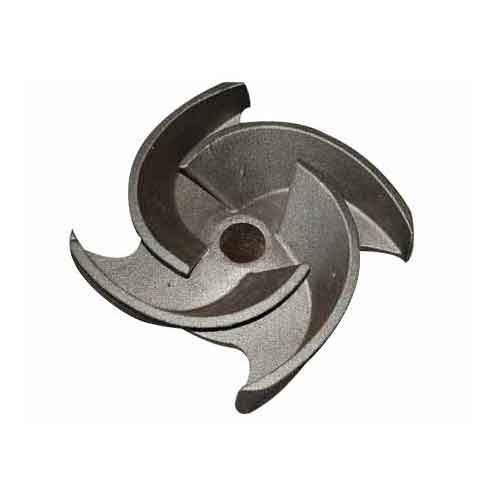
Circulation body impeller
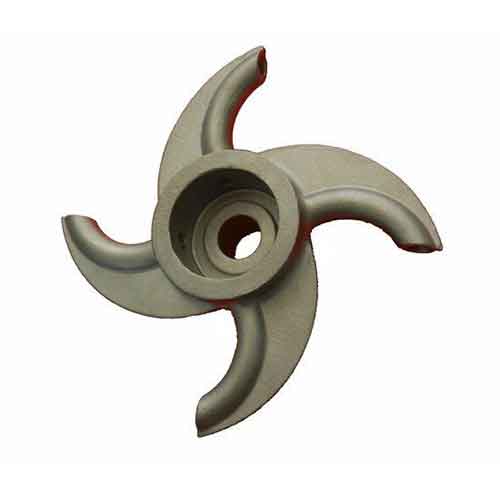
Custom made impeller for pump
The manufacturing methods of the impeller
Types of impeller
The optimal performance of a centrifugal pump is largely dependent upon its impeller design. An effectively designed impeller aims to enhance flow, reduce turbulence, and maximize efficiency. Impeller casting is commonly categorized into three main types: Open impeller, Semi-open impeller, and Closed impeller.
Open impeller |
An open impeller is a type of centrifugal impeller with vanes that are not covered by a shroud. In other words, the impeller’s blades are exposed to the liquid being pumped. This design is typically used for low-pressure applications where the pumped fluid contains suspended solids or fibers (such as waste water or pulp), as the open impeller is less susceptible to clogging or damage than a shrouded impeller. The open design also makes it easier to inspect and clean the impeller. However, open impellers are less efficient than shrouded impellers due to increased turbulence and leakage around the vanes. |
Semi-open impeller |
A semi-open impeller is a type of centrifugal pump impeller that has vanes on one side, leaving the other side open to the suction side of the pump. The fluid being pumped enters the impeller through the open side, and the vanes on the other side direct the flow outward to generate pressure and create flow. This design allows for the passage of solids and other debris through the pump without clogging, making it ideal for applications that involve fluids with high levels of solids or other particulate matter. |
Closed impeller |
A closed impeller is a type of impeller used in centrifugal pumps. It consists of a circular plate with curved blades mounted on it. The blades are arranged in such a way that they form a completely enclosed chamber, with no space between them. This design allows the fluid to be pumped efficiently with minimal losses due to turbulence and backflow. Closed impellers are used in high-pressure and high-volume applications where the fluid being pumped is clean and free of abrasive particles. They are also used in applications where the fluid contains small or fine particles that could clog an open impeller. |
How to make impeller with investment casting?
Bellow video shows how investment casting impeller making.
- Design the Impeller: First, design the impeller to be cast with precision and accuracy, with important features like its size, shape, and the number of blades.
- Create a Mold Pattern: Create a mold pattern made of wax or plastic that will be the exact replica of the impeller. This will be used to create the investment mold.
- Coat the Mold Pattern in Ceramic: Dip the mold pattern into a liquid ceramic slurry and dry it. Repeat this process several times, each time increasing the thickness of the ceramic coating.
- Burn Out the Wax: Once the final ceramic coating has dried, place the mold in a kiln to burn out the wax and any other impurities, leaving a hollow ceramic mold.
- Pour the Molten Metal: Once the mold is cleaned and prepared, pour molten metal into it. Allow to cool and solidify.
- Break the Mold: After the metal has cooled and solidified, break the ceramic mold to reveal the investment cast impeller.
- Finish the Impeller: Remove any excess material and finish the impeller to the desired shape and surface finish.
- Quality Check: The final step is to inspect the impeller for any defects and ensure it meets the required specifications.
Commonly used stainless steel for investment casting impeller
- AISI 316 – This stainless steel grade is known for its excellent resistance to corrosion and high-temperature resistance. It is commonly used in marine applications and in the chemical processing industry.
- AISI 304 – This is another commonly used stainless steel grade for impeller casting. It is known for its good corrosion resistance, weldability, and forming properties.