Engine impeller production with metal casting negative pressure filling
Shrinkage, Insufficient casting and low density are common casting defects in precision casting. The negative pressure filling-pressure solidification process is used to pour the engine impeller. Not only can eliminate the above defects, but also be more significant in the production of thin wall parts, complex parts and large precision parts, with good filling ability. The integrity of the casting is incomparable to that of ordinary gravity casting. Greatly improve the density, metallographic organization and mechanical properties of aluminum alloy castings.
At present, the qualified rate of finished casting is not high in many precision casting plants. This will lead to lower quality grade and high added value. To become bigger and stronger, in addition to improving the level of process control, at the same time, we must take the development path of process innovation and equipment improvement.
- Structural analysis of the casting parts
The structural shape of the engine impeller, see Figure 2-67. Its main body is composed of two internal and external cylinders, and the wall thickness of the two cylinders is almost the same. There are two impeller in the cylinder, and 16 blades are distributed in the small cylinder.22 blades are distributed in the big cylinder. The blade shape has a curved surface. Blade thickness is 1.2mm. The thin section of the blade should ensure its high size accuracy. Blade roughness, R3.2. The impeller height size is 164mm. Large round outer diameter of 350mm. The casting has a single weight of 9kg.
The engine impeller is made of aluminum alloy, with the brand name of A356. The quality of the casting requires that except for no casting defects, the repair is not allowed, and welding is not allowed on the casting blade. Each leaf shall be 100% through fluorescent detection.
The biggest difficulty of this structure is the uneven wall thickness. The blades are particularly thin, distributed in separate layers, and the number of blades is large. The integrity of the filling is problematic.
If centrifugal casting is adopted, it is difficult to implement due to the inconsistent rotation direction of the blade surface. Conventional gravity casting simply does not guarantee the mass production quality. The rejection rate is quite high. According to the analysis, the pouring process of negative pressure filling-pressure solidification must be used to meet the quality requirements of such products.
2. Pattern assembly
The wax pattern of the engine impeller is made of low-temperature die. Pattern assembly scheme is shown in Figures 2-67. The upper and lower parts of the impeller are equipped with “cross shaped” transverse runners, which are connected to the suction casting rod.
the lower part of the impeller inner cavity, there is a section of 82mm height and 50mm diameter. The upright straight pouring channel is connected to the conical cylinder solid plane. The other end of the direct pouring channel (the negative pressure filling rod) is connected with the upper transverse pouring channel.
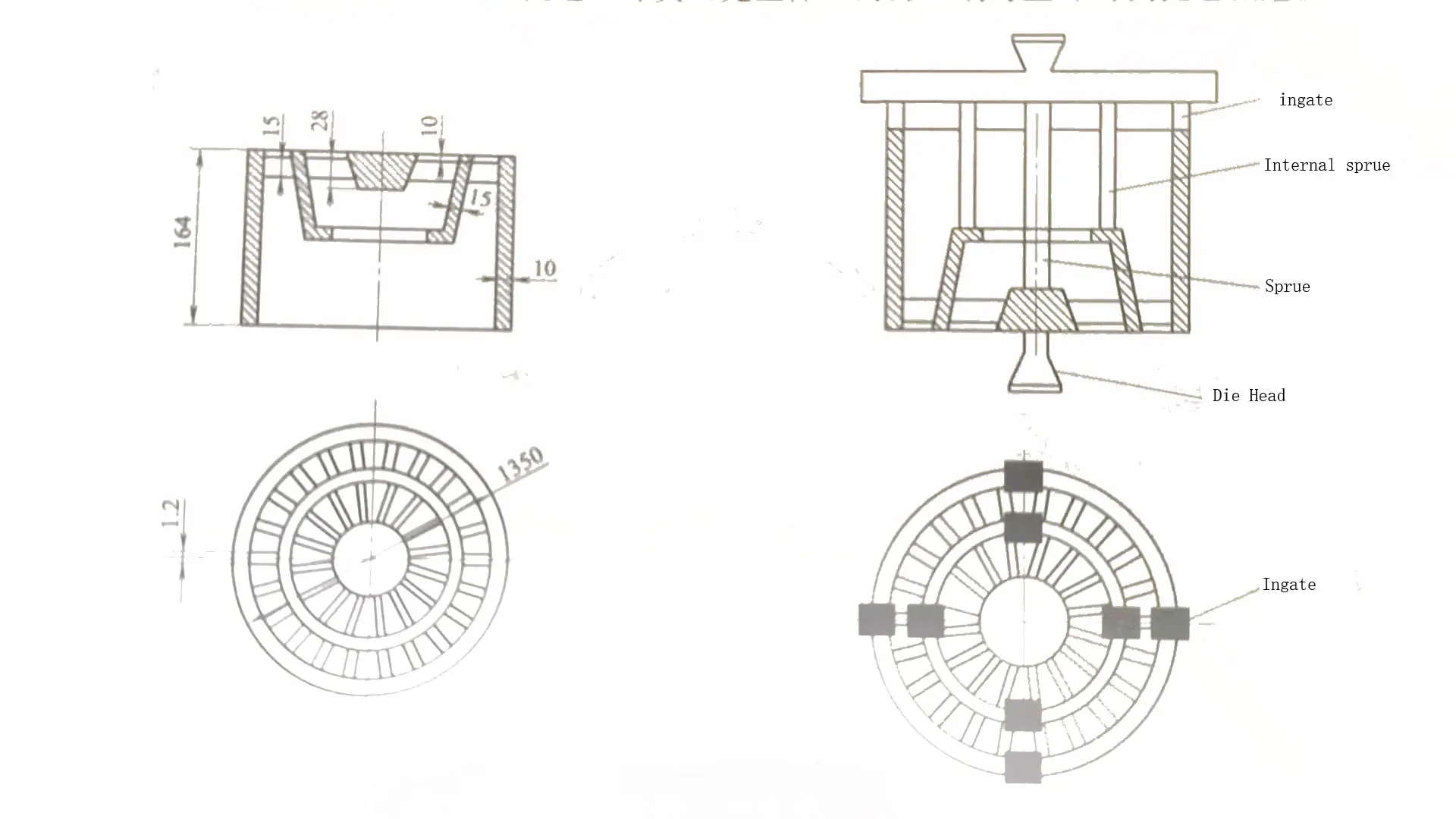
The negative pressure filling rod is in the center position, and the “cross shape” horizontal pouring channel is connected with it. The whole module has a well-established rigidity. The charging rod used in the negative pressure charging process (commonly used in molten mold casting) is characterized by two watering cups at both ends and two wooden handles at both ends. The middle of the pouring rod is either square or round.
3. Shell making and Calcination.
The shell making adopts the conventional all-silicon sol shell making process. Apply the double-sided layer with zirconium powder paste and zirconium powder sand. The mass ratio of surface slurry powder is 3.9 to 1. The viscosity value of the second layer of zirconium powder is 25, pre-immersion. From the third layer begin with mollai powder, mollai mortar coating. Usually six layers are OK. Strength is enough. However, using the negative pressure filling -pressure solidification process, the coating must be eight and a half layers.
4. Negative pressure and pressurization
Negative pressure filling-pressurized solidification furnace is divided into two parts. The cover plate of the furnace belongs to the lower part of the furnace, and the upper part is the furnace body part of the furnace. The smelting, metamorphic, refining, adjustment of element composition, and the insulation of metal liquid are completed in the lower smelting pool. After the pure aluminum alloy solution is prepared, cover the furnace cover plate on the melting pool furnace surface. The negative pressure tube is also inserted into the molten tank. Then place the mold shell after roasting and insulation. Then, the furnace body and the furnace cover plate are docked and closed on it. At this time, the preparation work before the negative pressure filling is completed.
5. Final Casting parts
Using the melting mold casting process to make the shell, the negative pressure filling type-pressure solidification pouring process, the perfect pouring out of the aluminum alloy engine impeller sample. Through the strict quality acceptance, and stable to put into mass production.
shell removal after pouring is generally no difficulty. Because of the use of zirconium powder and zirconium sand to do double-sided coating, so the mold shell is easy to clean. The qualified rate of casting for finished products is above 95%.
American standard cast aluminum alloy A356 is the Al-Si series. The alloy elements are low, Cu <=0.25%, Mn <=0.35%, Mg0.2%, Zn <=0.35%, the density is 2.68 g/cm3. Due to the tight internal structure of the engine impeller poured with negative pressure filling-pressure solidification equipment. The density of the casting reaches 2.7. When the casting is knocked, it produces a clear sound of steel.