Solution to Shrinkage Defects on Threaded Covers in Automotive Casting
In the production of investment casting automotive casting parts, shrinkage defects often occur on the castings. The occurrence of shrinkage defects is generally related to three aspects: casting structure, pouring system, and process design. In the analysis and resolution of shrinkage defects, it is important to follow the theory of temperature gradient, analyze the specific structural characteristics of the casting, and correctly implement thermal gating and continuous improvement.
The main difference of investment casting automotive casting parts compared to other casting methods is that it is poured under the condition of a ceramic shell (shell firing temperature around 1100℃). This allows for good filling capability, but it also presents challenges in terms of compensating for the shrinkage of the casting. In addition to using computer numerical simulation analysis, it is necessary to consider the temperature gradient during the cooling of the casting and adopt comprehensive strategies based on the structural characteristics of the casting. Continuous improvement is imp
ortant. In this particular case, the focus is on addressing the shrinkage issues of isolated hot spots.
(1) Introduction of the investment casting automotive casting parts
Part name: Threaded cover, made of material 304. The dimensional accuracy and surface quality requirements are high. The weight of a single piece is 0.5kg. The schematic diagram of the casting can be seen in Figure left.
(2) First Pouring Process
Figure 6-50 shows the inner gate of the wax mold for the threaded cover, placed on a flat surface with a diameter of ø78mm and set symmetrically in two positions. Figure 6-51 shows the shape of the inner gate. There are two tree assembly schemes for the investment casting automotive casting parts: one with a horizontal mold head and the other with a vertical mold head. The shell is made using a mid-temperature wax, all-silica sol process, with a shell firing temperature of 1150℃ and insulation for 30 minutes. The pouring temperature is 1670℃. Prior to pouring, computer numerical simulation analysis was carried out, which did not reveal any shrinkage defects. However, serious shrinkage defects were observed during actual production using both the horizontal and vertical mold heads.
6-50 Internal gate position
6-51 The shape of the inner gate
6-51 Horizontal mold head group tree scheme
6-51 Vertical mold head group tree scheme
(3) The investment casting automotive casting parts Shrinkage analysis
Originally, it was believed that the complexity of the component was average. After the first pouring, a re analysis of the casting structure was conducted, and it was believed that the overall structure of the component was a thin-walled component. However, there is a flange shaped protrusion in the middle of the threaded cover, which has three stepped plane hierarchical structures.
In automotive casting production, wall thickness variations significantly impact quality. The measured dimensions show the first layer plane at 2.86mm, second layer at 4.98mm, and third layer at 9.26mm – a substantial differential that creates challenges in automotive casting processes. Shrinkage defects typically appear at the threaded protrusion root due to the maximum wall thickness area forming an isolated hot spot with adjacent thin-wall sections.
For optimal automotive casting results, the solidification process requires careful temperature gradient management. The thin-wall threads should cool first, while the thickest protrusion section (third stage at 9.26mm) must solidify last to maintain proper sequential solidification. This automotive casting principle ensures sufficient molten steel remains available to compensate for cooling shrinkage, preventing defects near critical threaded areas.
The casting methods illustrated in Figures 6-52 and 6-53 demonstrate successful automotive casting techniques worth preserving: vortex-free pouring, smooth steel flow, complete mold filling, and high production yield. These factors are particularly valuable when manufacturing precision automotive casting components with complex geometries and varying wall thicknesses.
At the same time, it is analyzed that the baking temperature of the investment casting automotive casting parts mold shell in the first pouring process is relatively low, the insulation time is still acceptable, and the pouring temperature of the steel liquid is too high, which violates the principle of “low-temperature steel liquid, red shell pouring”.
(4) Process improvement
In automotive casting processes, establishing a proper feeding channel is crucial to supply molten steel to flange-shaped protrusions. For optimal results in automotive casting production, we implemented an 8mm straight riser strip between the mold head and protrusion (as illustrated in the right figure). Additionally, we optimized the automotive casting parameters by increasing the shell mold calcination temperature to 1180℃ (held for 30 minutes) while reducing the pouring temperature to 1650℃. These adjustments in the automotive casting process significantly improve feeding efficiency and reduce shrinkage defects in critical components.
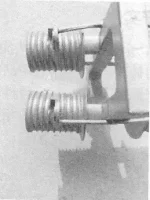
Pouring result: Shrinkage has not been completely eliminated in the final investment casting automotive casting parts, but the range of shrinkage has significantly decreased and the depth of shrinkage has also become shallower. The analysis and judgment on the occurrence of shrinkage defects are correct, which further confirms that the added straight bars are too small and not in place. Ultimately, there is a lack of depth in understanding that different parts of the casting should have different cooling rates, and the adjustment of cooling rates is not well controlled by temperature gradients.
(5) Continuous improvement
A small plane of 9mmx9.5mm was found on the side of the third level of the flange shaped protrusion, which was selected as the location for the inner gate. The shape of the inner gate is shown in Figure below. The bottom size of the inner gate is 9mm long x 9.5mm wide x 12mm high, and it is made into a cone. Due to the small size of investment casting parts, the inner gate in the pouring system is generally not only the gate that connects the casting, but also serves as a riser, establishing a temperature gradient, allowing the investment casting automotive casting parts maximum wall thickness of the protrusion to be compensated, and sequentially solidifying and finally cooling.
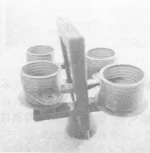
In automotive casting processes, rapid filling of thin-walled components is critical. Therefore, we maintained the secondary inner gate at its original φ78mm plane position, connecting it via optimized straps for efficient metal flow. This automotive casting solution ensures proper filling while minimizing turbulence.
To enhance automotive casting production efficiency, we replaced the conventional bifurcated mold head with a purpose-redesigned version specifically for this application. The optimized internal gate configuration (as illustrated in the left figure) demonstrates our automotive casting expertise in gating system design, balancing filling speed with casting quality requirements.
After continuous improvement of the pouring system, the shrinkage holes on the threaded cover on the investment casting automotive casting parts were completely eliminated. From the cutting section of the internal pouring, the shrinkage effect was quite successful, and the yield rate reached 100%.