Characteristics and Importance of Sand Casting Process
Sand casting represents one of the most versatile and widely utilized metal casting processes in modern manufacturing, where molten metal alloys are poured into precisely formed sand molds to create durable metal components across virtually every industrial sector.
As an experienced sand casting manufacturer based in China, our foundry specializes in this time-tested production method that delivers cost-effective solutions for both simple and complex part geometries. While the majority of cast components require some degree of machining to achieve final dimensional tolerances, sand casting provides distinct advantages in producing near-net-shape parts with exceptional material properties and structural integrity. The process begins with pattern creation, followed by mold formation using specialized sand mixtures, careful metal pouring and solidification, and finally mold removal to reveal the finished casting.
This fundamental manufacturing technique has remained indispensable due to its unique combination of design flexibility, material versatility, and production scalability that meets the demanding requirements of industries ranging from automotive and heavy machinery to energy generation and aerospace applications.
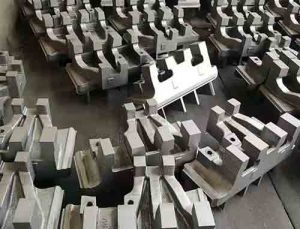
The industrial significance of sand casting becomes evident when examining the weight percentage of cast components within various types of machinery and equipment. In heavy industrial applications such as machine tools, internal combustion engines, and construction machinery, sand cast parts typically constitute between 70-90% of total machine weight, demonstrating their critical structural role.
The agricultural equipment sector relies on sand castings for 40-70% of component mass, while automotive systems incorporate 20-30% cast parts including essential elements like engine blocks, transmission housings, and suspension components. This widespread adoption extends across mining equipment, hydroelectric turbines, petrochemical processing systems, industrial pumps and valves, railroad components, marine hardware, and even artistic installations – virtually no sector of modern manufacturing operates without depending on sand cast metal parts.
The process’s ability to produce components ranging from miniature precision elements weighing mere grams to massive industrial castings measuring several meters in length and weighing multiple tons makes it uniquely suited to serve diverse production needs while maintaining consistent quality standards.
When compared to alternative metal forming processes, sand casting offers several distinct technical and economic advantages that explain its enduring popularity in industrial manufacturing. The process demonstrates unmatched material flexibility, capable of working with virtually all castable metal alloys including various grades of cast iron, carbon and alloy steels, aluminum, copper, magnesium, and specialized high-performance alloys developed for extreme operating conditions.
From a design perspective, sand casting accommodates complex geometries that would be impossible to produce through machining or forming processes, including intricate internal passages, variable wall thicknesses, and customized surface textures. The economic benefits prove equally compelling, with significantly lower tooling costs compared to die casting or forging processes, making sand casting particularly advantageous for both prototype development and medium-to-high volume production runs. Modern foundry techniques have further enhanced these inherent advantages through innovations like 3D printed sand molds for rapid prototyping, advanced simulation software for process optimization, and automated molding systems that improve consistency while reducing production costs.
As a professional sand casting service provider, our China-based foundry combines these technological advancements with decades of practical experience to deliver high-quality cast components that meet the exacting standards of global manufacturers across every industry that depends on durable, precision metal parts.
The continued evolution of sand casting technology ensures its relevance in an increasingly sophisticated manufacturing landscape, with ongoing developments in mold material science, melting and pouring techniques, and quality control systems pushing the boundaries of what can be achieved through this ancient yet constantly improving production method.
Environmental considerations have also driven significant progress, with modern foundries adopting more sustainable practices including sand reclamation systems, energy-efficient melting furnaces, and eco-friendly binding agents that reduce the process’s environmental footprint without compromising part quality. These advancements, combined with the process’s inherent flexibility and cost-effectiveness, guarantee that sand casting will remain a cornerstone of industrial manufacturing for decades to come.
As a trusted sand casting manufacturer serving clients worldwide, we remain committed to advancing this vital production technology while maintaining the highest standards of quality, precision, and reliability that our customers have come to expect from our foundry services. Whether producing prototype components or high-volume production runs, sand casting continues to offer manufacturers an unparalleled combination of technical capability and economic efficiency that few other metal forming processes can match.