Handle Casting
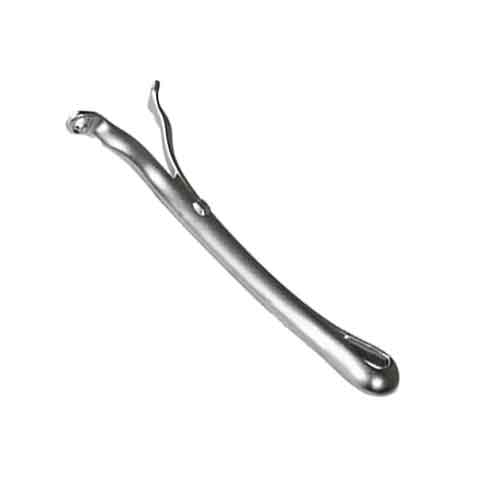
Kitchen pot handle casting
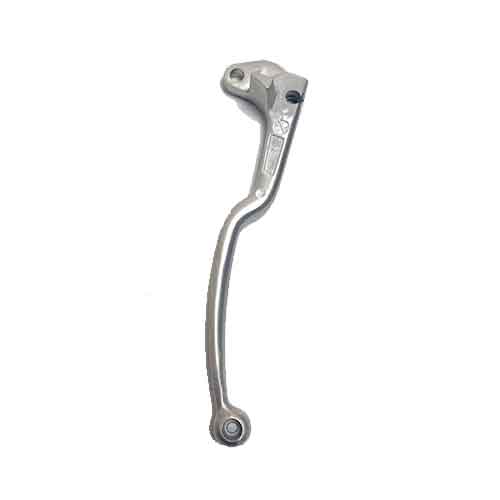
Motorcycle handle casting
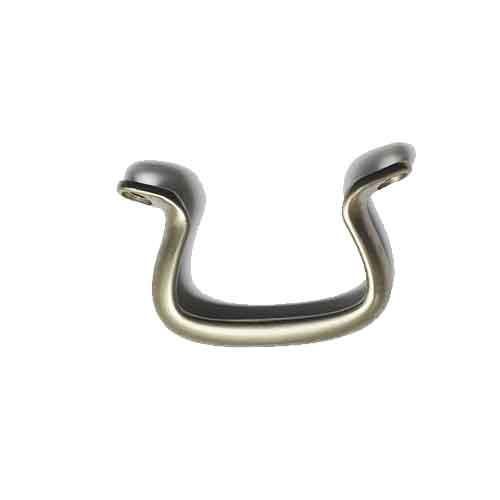
Steamer handle casting
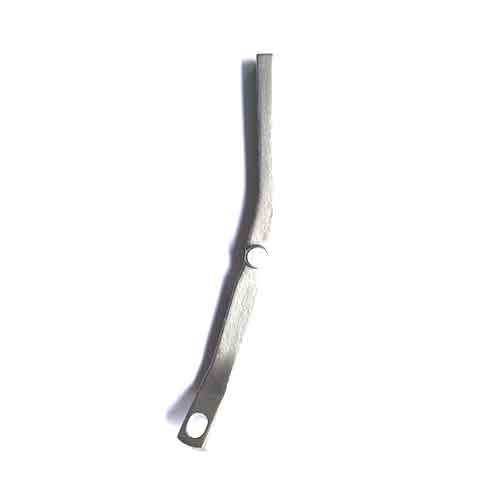
Mechanical handle casting
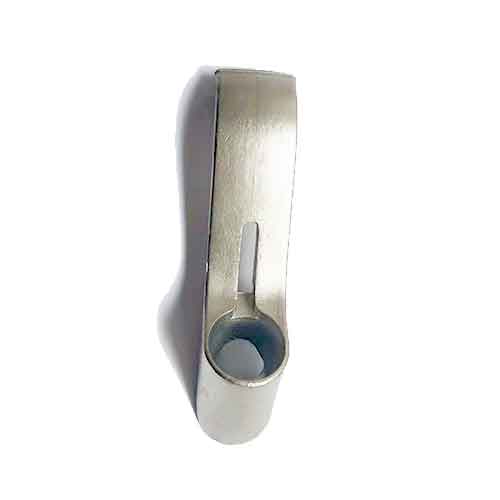
Faucets handle casting
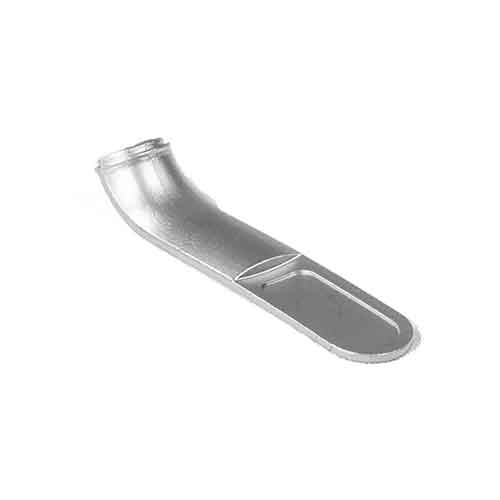
Hardware handle casting
Different Types of Handle Casting:Comparison of different handle casting methods
There are different handle casting methods, including sand casting, die casting, investment casting, and gravity casting. These methods all have their unique benefits and drawbacks.
1. Sand Casting for Handle Casting
Sand Casting Handles
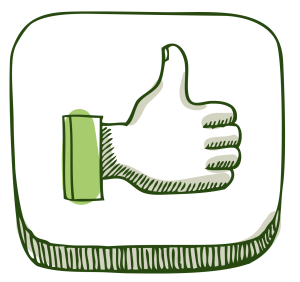
Advantages
– Low cost of production
– Suitable for making large batches of handles
– Sand molds can be easily customized to create different handle designs and shapes.
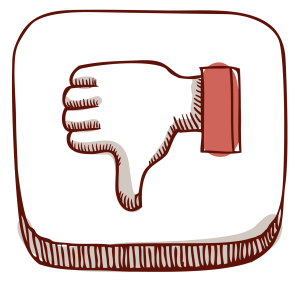
Disadvantages
– Surface finish is rough compared to other casting methods.
– The process is labor-intensive and time-consuming.
– The risk of sand contamination by the molten metal.
2. Die Casting for Handle Casting
Die casting is a precision method used in handle casting, where molten metal is injected into a mold under high pressure. As a leading handle casting manufacturer and supplier in China, Chongqing Sipx Machinery excels in this technique.
The mold, a crucial component of this process, consists of two parts: the cavity and the ejector. Our advanced foundry equipment ensures precise mold design and manufacturing, guaranteeing high – quality handle production.
Once the molten metal is injected into the mold and solidifies, the ejector plays a vital role in pushing the casting out. This step requires precision and care to ensure the handle’s integrity and quality.
Die casting is ideal for producing intricate handle designs and shapes that require high precision. At Chongqing Sipx Machinery, we leverage this method to create handles with complex details and tight tolerances, meeting diverse customer needs.
As a professional foundry supplier, we are committed to delivering exceptional service and high – quality handle casting products. Our die casting service combines advanced technology with rigorous quality control standards, ensuring that each handle meets the highest specifications.
Whether you are sourcing from China or other regions, we are ready to provide you with reliable handle casting solutions that match your specific requirements. Our expertise in die casting makes us a trusted partner for businesses seeking precision and quality in handle production.
Die Casting Handles
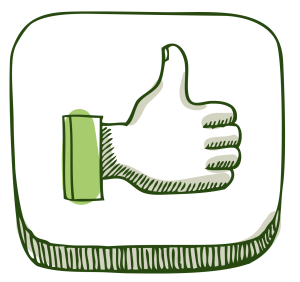
Advantages
– Accurate dimension and high precision in handling small parts
– Smooth surface finish
– Suitable for mass production of handles
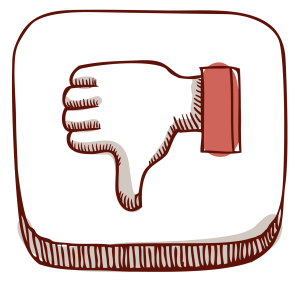
Disadvantages
– High initial cost of equipment and tooling
– Limited to certain alloys due to the high pressure
– Weaker casting because of the high pressure, which can cause porosity.
3.Investment Casting for Handle Casting
Investment Casting Handles
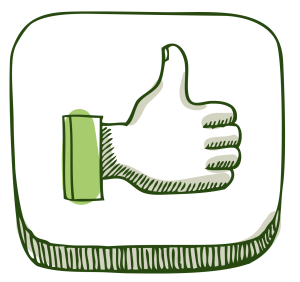
Advantages
– Excellent surface finish and high accuracy
– Can produce complex and intricate handle designs
– Suitable for high-quality production of smaller batches
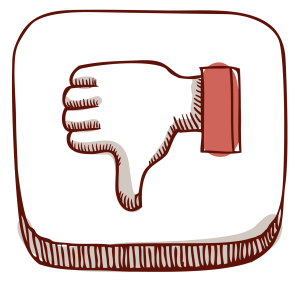
Disadvantages
– High setup cost
– Time-consuming
– Limited to smaller handle sizes
4.Gravity Casting for Handle Casting
Gravity casting is a significant method in the field of handle casting. As a China-based manufacturer and supplier, Chongqing Sipx Machinery has extensive experience in this technique.
This method involves pouring molten metal into a mold using gravity to fill the mold. The mold can be made of sand, clay, or other suitable materials. Our foundry carefully selects the mold material based on the specific requirements of the handle design and production volume.
Gravity casting is particularly suitable for producing handles with simple designs and shapes. It offers several advantages, including lower production costs and shorter lead times compared to more complex casting methods. At Chongqing Sipx Machinery, we optimize the gravity casting process to ensure consistent quality and efficiency.
Our skilled workers meticulously control the pouring process to ensure the molten metal fills the mold evenly and completely. This attention to detail results in handles with good surface quality and dimensional accuracy.
As a professional foundry supplier, we are committed to providing high-quality handle casting products and exceptional service. Whether you are sourcing from China or other regions, we are ready to meet your handle casting needs with reliable solutions that match your specific requirements.
Gravity Casting Handles
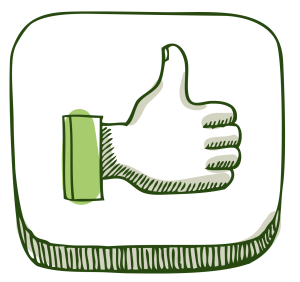
Advantages
– Compared to sand casting, it produces a better finish
– Suitable for casting a wide range of metals alloys
– Faster production time than sand casting
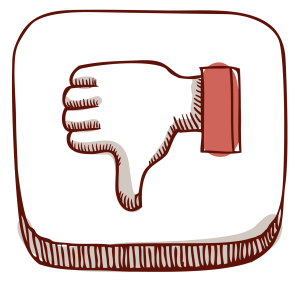
Disadvantages
– Lower precision and accuracy
– Limited to producing handles with simple shapes
– Not suitable for large batches of handles.
Types of materials used for handle casting
Materials |
Detail |
Aluminum |
Aluminum is a lightweight and durable metal that is commonly used in handle casting. It is corrosion-resistant and can be easily recycled. |
Brass |
Brass is a copper-zinc alloy that has a distinctive golden color and is easy to cast. It is also corrosion-resistant and has a long life span. |
Aluminum |
Cast iron is a durable material that is commonly used for pump castings. It is strong, resistant to wear and tear, and has good fluid-carrying capabilities. |
Zinc alloy |
Zinc is a low-cost metal that is used in handle casting because of its durability and corrosion-resistance. It can be easily molded into complex shapes and has a shiny finish. |
Stainless Steel |
Stainless steel is a corrosion-resistant alloy that is commonly used in handle casting. It has a unique ability to resist stains and is easy to maintain. |
Bronze |
Bronze is a copper-tin alloy that is commonly used in handle casting. It has a beautiful brown color and is resistant to corrosion. It is widely used in the casting of decorative handles. |
Post processes for handle casting
-
Cleaning and Inspection – After the casting process, the handle needs to be cleaned thoroughly to remove any dirt, debris, or residuals. Our workers carefully clean each handle, ensuring no impurities remain. The handle is then inspected for any imperfections or defects that may have occurred during casting. We use advanced inspection equipment and strict quality control standards to identify and address any issues.
-
Surface Finishing – Improving the appearance and feel of the handle is crucial. Surface finishing involves various processes such as sanding, buffing, and polishing. These steps not only enhance the handle’s visual appeal but also improve its tactile quality. Our skilled technicians ensure a smooth and consistent finish on every handle.
-
Machining – In some cases, the handle may need to be machined to achieve a specific shape or to remove excess material. Our advanced machining equipment and experienced operators ensure precision and accuracy in this process. Machining helps refine the handle’s dimensions and meet tight tolerances.
-
Heat Treatment – Depending on the material used, the handle may undergo heat treatment to increase its strength and durability. Our foundry has specialized heat treatment facilities to optimize the material properties of the handles. This process ensures that the handles can withstand the stresses and strains of their intended applications.
-
Coating or Plating – To prevent corrosion, enhance appearance, or improve performance, a handle may require a protective coating or plating. We offer various coating and plating options to meet different customer requirements. Our coating processes are designed to provide long – lasting protection and aesthetic enhancement.
-
Assembly – For some handles, additional components such as screws or fasteners need to be added before the handle is ready for use. Our assembly team ensures that all components are properly installed and securely fastened. This step is crucial for the handle’s functionality and performance in its intended application.
-
Quality Control – Before any handle is released to the market, it undergoes rigorous quality control checks. We have a dedicated quality control team that ensures each handle meets the required standards and specifications. Our commitment to quality ensures that our customers receive reliable and high – performance handle casting products.
Different industries that use casting handles
-
-
Automotive Industry: As a professional manufacturer and supplier from China, we specialize in handle casting for the automotive industry. Casting is a widely utilized process in this sector, especially for creating vital components like engine blocks, cylinder heads, and transmission cases. Our high – quality handle casting services ensure the precision and durability required in automotive parts, meeting the rigorous standards of the industry.
-
Aerospace Industry: In the aerospace field, handle casting plays a crucial role. The aerospace industry extensively uses casting for producing engine components, wing structures, landing gear, and more. Our company, a reputable China – based foundry, offers top – notch handle casting services. We understand the stringent requirements of aerospace parts and are committed to delivering castings that meet the exact specifications and quality demands of this high – tech industry.
-
Jewelry Industry: When it comes to the jewelry industry, casting is an indispensable technique. We provide excellent handle casting services for manufacturing various jewelry items such as rings, pendants, and earrings. Casting proves to be a cost – effective and efficient method for producing large quantities of jewelry. As a reliable supplier from China, we leverage our expertise in casting to help jewelry businesses create beautiful and intricate pieces while maintaining cost efficiency.
-
Medical Industry: The medical industry has specific needs for precision and reliability, which our handle casting services can meet. Casting is employed for producing a range of medical instruments, implants, and prosthetic devices. As a China manufacturer with extensive experience in foundry work, we supply medical – grade castings that comply with strict health and safety standards. Our commitment to quality ensures that the castings we produce can be trusted in critical medical applications.
-
Construction Industry: In the construction sphere, handle casting has its unique applications. The construction industry uses casting to create various architectural elements like cornices, columns, and balustrades. Our company, being a qualified supplier and foundry in China, offers custom handle casting services to meet the diverse needs of construction projects. We can produce castings that match specific architectural designs and requirements, contributing to the aesthetic and functional aspects of buildings.
-
Marine Industry: For the marine industry, handle casting is essential for manufacturing numerous marine components. We are adept at providing handle casting services for parts such as propellers, anchors, and other marine accessories. As a trusted China – based foundry and supplier, we recognize the harsh operating conditions of marine equipment and strive to produce castings with excellent corrosion resistance and strength to withstand the marine environment.
-
Electrical Industry: Casting is extensively used in the electrical industry, and our handle casting services are well – suited for this purpose. We produce various electrical components like electrical switchgear, transformers, motor housings, and other parts through casting. As a professional manufacturer and supplier from China, we ensure the electrical performance and safety of our castings, meeting the industry’s standards for insulation, conductivity, and durability.
-
Sporting Goods Industry: The sporting goods industry benefits greatly from handle casting. We offer specialized handle casting services for manufacturing components of sporting goods such as golf club heads, fishing reels, and other sports equipment. As a China – based foundry with a focus on quality and innovation, we collaborate with sporting goods companies to create castings that enhance the performance and durability of sports equipment, meeting the demands of athletes and sports enthusiasts.
-
Chapter 1
Knowledge about handle casting
1.1- The application of box fastening to create a reducing atmosphere in investment handle casting
After pouring carbon steel handles, American standard 200 series, and 400 series stainless steel handles, the surface quality of casting handle parts can be seriously affected by secondary oxidation of the steel liquid. This leads to defects such as decarburization, concave-convex patterns, and pitting, which can compromise the overall quality of the product. To avoid these defects, a number of measures can be taken during the casting process.
One effective solution is to use combustible materials such as waste wax and sawdust to create a reducing atmosphere around the steel liquid. After pouring the steel liquid, a fixed amount of these materials can be placed on the sprue cup of the mold shell. The mold shell can then be quickly covered with an iron box to prevent the steel liquid from contacting the air and producing oxidation.
In this way, an atmosphere of carbon dioxide and carbon monoxide can be created from the incomplete combustion of the combustible materials. This allows the steel liquid to slowly cool and solidify in a reducing atmosphere, reducing the thickness of the decarburization layer on the surface of the casting handle parts. It also eliminates concave-convex patterns and pitting defects, which is beneficial for refining the surface of the casting handle parts.
This process is particularly important for casting handles made of steel materials with high chromium content for a steel casting manufacturer, such as the American standard 200 series and 400 series stainless steel handles. When these materials are poured at high temperatures, they are prone to secondary oxidation, which can lead to a range of defects that affect the surface quality of the product.
By using combustible materials to create a reducing atmosphere during the casting process, manufacturers can ensure that the surface of casting handle parts is of high quality and free from defects. This not only enhances the overall appearance of the product but also improves its durability and longevity. As such, it is an important consideration for any manufacturer looking to produce high-quality casting handle parts.
Figure 5-23 shows the component diagram of the handle casting product of the American Standard 200 series. Figure 5-24 shows the process diagram of the product group, with a product number of 201 and chemical composition: C≤0.15%, Si≤1.00%, Mn5.5%~7.5%, P≤0.06%, S≤0.03%, Cr16%~18%, Ni3.50%~5.50%.
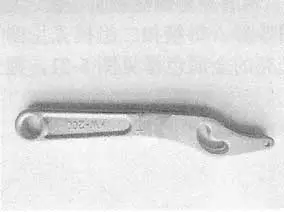
Figure5-23 handle casting part
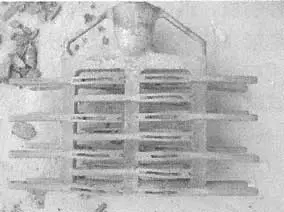
Figure5-24 handle casting tree assembling
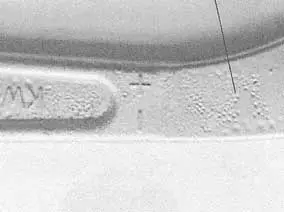
Figure5-25 handle casting defects

Figure5-26 handle casting defects disappeared
This piece uses a full silica sol shell making process, with 4.5 layers of shell. The handle shell is baked at a temperature of 1050-1150℃ for 30 minutes, and the new melting material usage is 60%. The steel material is clean, free of oil stains and corrosion.
Manganese iron 0.2%-0.3% is added at 1520℃, and silicon iron 0.2% is added at 1550-1570℃ for pre-deoxidation. After pre-deoxidation is completed, the temperature is raised to 1630-1650℃, and 0.2% silicon calcium manganese deoxidizer is added in three times with an interval of 5-10 seconds, followed by covering with a slag remover.
The temperature is raised to the pouring temperature and then the power supply is shut off for static settling. The static settling time of the molten steel is extended to over 3 minutes to ensure that inclusions fully float to the top, followed by multiple slag removals. The pouring temperature is 1600-1610℃.
After casting the handle product, due to the high chromium content and strong chemical activity of chromium, many dense circular light brown spots appear on the surface near the inner sprue, which are called pitting defects. The pits are regular hemispherical small pits, about 0.3-0.5mm deep, and filled with slag material before cleaning. Energy spectrum analysis of this material shows that it mainly consists of chromium oxide and silicon oxide. This type of defect often occurs in alloy steel castings with Cr20%, Ni10%. Although this defect does not affect the use of the handle casting, it cannot be repaired and is unacceptable to customers. The pitting defect becomes larger, as shown in Figure 5-25.
The reason is the secondary oxidation of the steel liquid during the cooling and solidification process. The chromium content of the 201 material is relatively high, and chromium reacts easily with oxygen to form inclusions. During pouring, the mold shell pouring temperature is about 900℃, and the pouring temperature of the steel liquid is about 1600-1610℃.
At this time, the temperature contacting the surface of the handle casting is extremely high, and coupled with the steel liquid rushing into the cavity from the inner sprue, it causes overheating near the inner sprue and the metal liquid solidifies slowly. At this time, oxygen in the atmosphere easily reacts with the metal surface through the mold shell to produce oxide, which aggregates with inclusions in the steel liquid to form pitting. By reducing the mold shell pouring temperature of the handle casting, and covering with a box and lid, pitting can be prevented, as shown in Figure 5-26.
FAQs
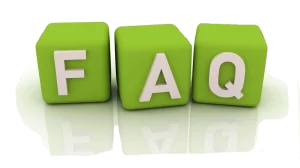
Handle casting is a process of creating handles for various objects by pouring molten metal or plastic into a mold. The mold is then cooled, and the resulting handle is removed from the mold and finished as required.
The tools and equipment required include a mold, a furnace or melting pot, a ladle for pouring liquid metal or plastic, a crucible for melting the material, and finishing tools such as grinders and sandpaper.
Objects that commonly use handle casting include cookware such as pots and pans, hand tools such as hammers and wrenches, and various types of equipment and machinery used in various industries.
We make precision casting parts according to clients drawings or samples. Faucets fittings, valve settings, automotive spare parts are common made in our foundry.
Materials commonly used for handle casting include metal alloys such as aluminum, copper, brass, and stainless steel, as well as plastics such as polypropylene and polycarbonate.
Handle casting offers many benefits, including the ability to create precise shapes and sizes, excellent durability and strength, and the ability to produce large quantities of handles in a short period of time. Additionally, handle casting is often more cost-effective than other manufacturing methods.
The production capacity of our precision casting foundry can produce 50000pcs per month.
We meet the ISO8062(GB/T6414) CT4-CT8 of Nominal dimension (mm) Linear dimension tolerance
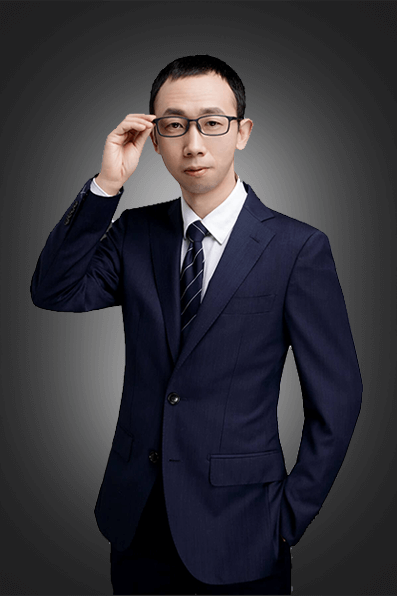
At SipxMach, our goal is to help our customers lower production costs and increase production rates and quality. Interested to see what SipxMach can do for you and your team? Contact us to schedule a tour of our state-of-the-art facility
- Contact: Rubio
- Email: [email protected]
- Microsoft Teams: Rubioli8677 (Sales manager)
- Office Add: No.551, Baosheng Avenue, Huixing Street, Yubei District, Chongqing, China
- Foundry Add: No. 4 Jindi Avenue, Dongcheng Street, Tongliang District, Chongqing